单件流生产方式是按产品别布置的多制程生产方式,产品在生产过程中实现单件流动,它是准时化生产的核心,是解决在制品的秘方,是消除浪费的最好方法。
单件流生产方式主要优点:
1.生产周期短:单件流生产方式采取分工原则,要求各工序不是批量生产后再流转下工位,而是生产一件(是否一件是最高效最经济需结合具体行业,以设定标准)就要流转下工位,并要求各工位按统一节拍生产,以实现生产过程顺畅,在制品不积压,快速得到成品,根据节拍和生产工时就可得知完成产量所需总周期,根据目标差异就可灵活应对,保障交货及时。
2.在制品少:单件流生产方式是连续流动生产,突出特点是在制品得以极大的压缩。
3.场地占用少:单件流生产方式极大的削减了在制品,减少在制品场地占用,工厂空间得以解放。
4.灵活性大:单件流生产方式,企业在制品总量极少,原材料的投入短周期内就转化为成品,对于客户需求变化的应对能力均大大提高,对于不同产品品种转换时间能大幅削减。
5.避免批量缺陷:单件流生产方式能快速出成品,各工位生产是有序衔接按节拍生产,通过本工序的自检和下工序的互检及质检员专检能及时发现各工序存在的质量问题,及时进行纠正,能有效避免批量质量缺陷。

单件流生产方式建立步骤:
步骤1 全员的意识建立:观念上必须改变,坚持以一个流生产方式作业,尤其是干部。
步骤2 成立示范改善小组:不同部门的中坚干部成立示范改善小组。
步骤3 选定示范生产线:应从最容易的地方下手作示范。
步骤4 现况调整分析:选定示范线后,应先充分分析产品的生产状况(如生产流程图,生产线布置方式,人员的配置,库存时间及设备稼动率等)。
步骤5 设定T.T时间:以每日的工作时数除以每日市场的需求数----即目标时间。T.T受出勤时间及订单量的变化而变化,与现场的设备、人员的生产能力是无关的。许多改善的出发点以T.T为依据。
步骤6 决定设备、人员的数量:根据T.T、各作业的加工时间和人力时间,计算出设备需求数和作业人员的需求数,设备不足,应分析稼动率,进一步改善以提高设备产能;而人员不足,则必须努力设法将零点几个人的工作量予以改善并消除掉。
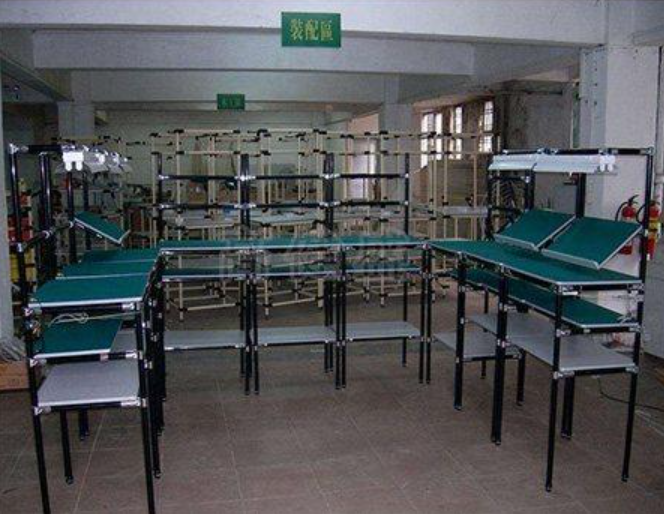
步骤7 布置一个流的生产线:根据作业加工顺序,以逆时针流动,设备尽量拉拢以减少人员走动及物品搬运的距离,设备小型化、滑轮化、专用化。
步骤8 配置作业人员:以“T.T”为目标,将各作业内容分配到每一个作业员,使得每一位作业员所分配到的作业时间的总和能无限接近“T.T”甚至完全一致。作业员必须要是多能工,才能有效充分的利用人力时间。
步骤9 维持十大污的软件与持续改善
步骤10 水平展开与少人化目标
本文为冠卓咨询原创文字作品,任何人或组织不得对本文进行篡改,转载或以盈利为目的行为,一经发现,将负法律责任。