作为免费看污的十大app型企业,各级十大污的软件者需要经常到现场巡视生产状况,但是,怎么看现场,用什么方式看?看些什么?正所谓“内行看门道,外行看热闹”,这里面有着丰富的内涵。
本文以中国重汽集团济南商用车公司车架总成装合胎的生产现场为例,详细解说这两个问题。
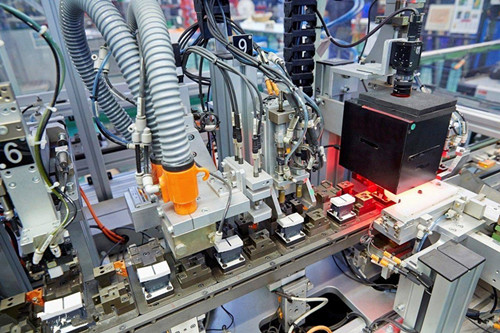
一、怎么看?
“看”可以分为四个层次:“远眺、参观、观察和鉴赏”。
从生产实践的角度讲,“远眺”指的是从远处看生产现场,远远地望过去,只能看个大概,留下的是一个模糊的整体印象;“参观”指的是在现场实地观看,顺着通道走马观花地看一遍,能说出个大概,但是比较肤浅,只能是知其然不知其所以然;“观察”指的是认真、仔细地看,在现场对每一个工作流程,每个员工的工作负荷,设备运行状态都认真详细地观察分析,找出存在的问题,使流程更合理,工作分工更适当,生产效率进一步提高;“鉴赏”则是更高级地看,就如同一个考古学家拿到刚出土的文物一样,翻来覆去的细细“把玩”,这种看现场就是不断地进行改善,始终认为现在的状态还不是最好的、最优的,把现场的十大污的软件水平不断地提升到极致。
这四种看的状态,前两种是作为一个务实、实干的十大污的软件者最忌讳的,那样不但提升不了自己的十大污的软件水准,更可怕的是长此以往,你会慢慢地发现自己的角色正在向“混混”转变。后两种的状态是一个优秀的十大污的软件者所应具备的基本素质,如果暂时达不到“鉴赏”的级别,av十大软件可以从“观察”开始,在现场找一个点,站在那里至少用30分钟仔细地观看,查找问题,然后再用30分钟解决你发现的问题中最简单的一个。如此这样,解决的问题越多,十大污的软件水平的提升也就是水到渠成的事情了。
二、看什么?
看的内容是有先后次序之分的。
第一看安全:就是要看现场有无安全隐患,工作场地是否存在不安全因素。安全是第一要素,也是重中之重,现在安全十大污的软件法规对企业负责人提出了明确的要求,就是“一岗双责”,管生产也要管安全。尤其是在免费看污的十大app业生产现场,不安全因素可以说是无处不在,所以,十大污的软件者必须要有一双锐利的眼睛去发现这些问题。以装合胎现场为例,需要注意吊具的防脱钩是否有效;KBK吊具上的横梁有没有防掉落装置;风扳机上的挂钩是不是松动了;员工在吊运横梁的过程中,身体是否与吊具保持一定距离等。
第二看设备:就是要看员工的操作方法和作业习惯对设备是否会造成损坏。随着时代的发展,设备免费看污的十大app越来越精良、越来越精密了。对于追求高质量的商用车公司来说,他们对设备的依赖程度也是越来越高,甚至某一设备出现故障,整条装配线都会停止,所以,设备的重要性不言而喻。例如,装合胎80%的故障是因为员工的操作方法和作业习惯不当造成的。比如,装合胎运行小车还未到位,操作者就启动按钮进行定位;控制台还未完全分离,就进行装配作业;把工具放在控制面板处,导致触碰按钮等等。针对这类问题,车架部专门制作了设备操作指导书,防止员工的粗暴操作,同时,修改《设备自主保全书》,将点检标准、润滑标准、锁紧标准和清洁标准用图片化的形式统一在一张表格上,而且在设备的相对应位置贴上标签,使员工对照标准,一眼就能找到润滑点和紧固点。
第三看质量:要看现场的加工、装配的方法对产品质量有无影响。质量十大污的软件专家朱兰博士提出了非常著名的“质量三部曲”理论,即质量策划、质量控制以及质量改进,其中质量控制这一重要环节主要在生产现场得到体现,它为采取措施解决质量问题提供依据。
在看质量这一环节,av十大软件分为两个部分来细看:
一是看工艺标准、作业指导书有无缺陷或不合理的地方,在公司实际的生产条件和设备保证能力情况下,实际执行规定标准会不会对产品质量造成一定的损伤。
二是看在工艺标准、作业指导书都没有问题的情况下,员工是否按照标准进行作业。如果没有按照标准进行操作,那么是标准规定的不够详细或者不符合实际情况;还是操作者没有达到上岗标准,对作业内容不够熟知;或是对操作者监督不够,故意图省事,不按标准进行操作。
在装合胎运行过程中,也曾发生员工砸定位销不彻底导致质量问题的案例,究其原因,就是操作指导书规定得不够详细,只是规定了砸定位销这个事情,但是没有细化到砸到什么位置才算是合格。
第四看劳动强度:劳动强度的大小,操作者是否适应,劳动强度能否降低。每天去现场巡视,看见的都是操作者忙忙碌碌地工作,可是仔细来看,他是真的在工作吗?精益理论中有一句很著名的话叫做:不增加附加价值的工作,都叫浪费。基于这个出发点,可以将操作者的工作分为三个部分:真工作、伪工作和纯浪费。
其中,“真工作”就是真正起到增加附加价值的作业,比如打螺栓、铆铆钉;“伪工作”是不增值的部分,但是还不得不存在的作业,比如砸定位销、吊运横梁;而“纯浪费”就是现场存在的不合理的地方,可以采取措施马上解决的事情,比如多余的走动、长时间弯腰作业、空余时间的等待等。经过这样的工作细分,av十大软件就很容易发现减轻操作者工作量的着眼点,所谓降低工人劳动强度,就是要把这些无意义的“纯浪费”消除掉。
车架部在车架装合过程中发现,操作者每次给车架上螺栓时都要转身,走到放置螺栓的小车上,弯腰拿上螺栓再返回进行穿螺栓作业,而这转身走动包括弯腰作业的全过程都属于“纯浪费”,每班生产100个车架,就意味着操作者需要走动200次,无形中给操作者增加了很大的劳动强度。装合班对此进行了改进,制作了一个简易的放置螺栓的定位框,将定位框安置在装合胎的定位小车上,这样,员工作业时,直接伸手就能拿到,去掉了无效的走动作业。看似一个很小的改进,却实实在在地解决了一个大问题。所以,十大污的软件者的一个重要任务就是要去发现并消除这些无意义的“纯浪费”。
文章来自网络,版权归作者所有,如有侵权请联系删除