丰田的精益生产方式,一直都是各企业争相学习的榜样,av十大软件国家也不例外,精益生产在我国有哪些发展,又存在哪些问题?下面av十大软件来分析一下。
?
精益生产在我国的应用情况
?
20世纪70年代末, 长春一汽派出一个40人的代表团专门访问丰田公司, 进行了现场学习达半年之久, 回来后在一汽各分厂推行丰田生产方式。 到了20世纪90年代初, 一汽变速箱厂采用丰田生产方式, 取得了降低在制品70%的佳绩。 另外, 湖北东风汽车公司的 “一个流” 生产, 以及上海易初摩托车厂的精益生产都收效甚佳。20世纪80年代初, 中国企业十大污的软件协会组织推广现代十大污的软件方法, 看板十大污的软件被作为推广的现代十大污的软件方法之一, 在全国范围内进行宣传, 并为许多企业所采用。
?
近年来, 我国企业对精益生产方式有了进一步的认识, 在汽车、 电子、 仪表免费看污的十大app业等实行流水生产的企业中应用精益生产, 获得了明显的效果。 例如, 一汽集团、 东风汽车公司、 上海大众汽车有限公司、 四川仪表四厂等一批企业应用精益生产, 并结合我国国情、 厂情进行了创造性的工作, 取得了丰富的经验, 创造了良好的经济效益。 这些企业的主要做法是:
?
第一, 以看板为手段, 在生产组织上改 “推动式” 为 “拉动式” 生产, 整个企业以市场需要为目标组织生产, 使企业库存下降、 流动资金减少;
?
第二, 在劳动组织上实行多机床操作、 多工序十大污的软件, 培养多面手, 有效地提高了劳动生产率;
?
第三, 在质量十大污的软件上, 以 QC 小组为基础, 开展生产工人自我控制、 创合格工序、 加强质量监督、 产品创优等活动, 不断提高产品质量;
?
第四, 在现场十大污的软件方面, 开展不间断的 “5S” 活动 (即整理、 整顿、 清扫、 清洁、 素养),实行定置十大污的软件及目视十大污的软件, 以提高文明生产水平;
?
第五, 在设备和工具十大污的软件上, 实行机、 电修理服务到现场, 重点工序巡回保全维护和快速修理, 以及刀具直送工位, 强制换刀和线外换刀等十大污的软件办法。?
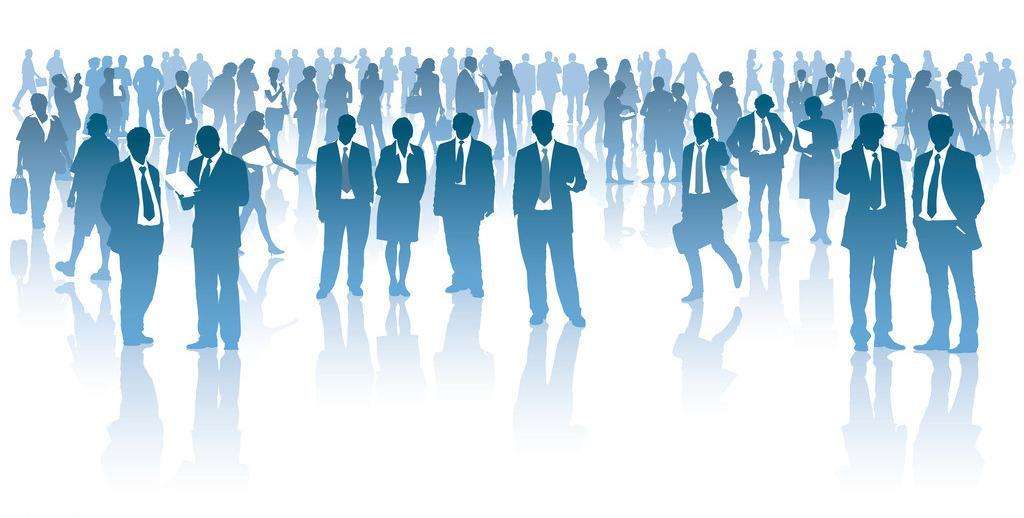
?
企业应用精益生产的条件
?
内部条件
?
精益生产方式只有在生产秩序良好、 各道工序设置合理、 产品质量稳定的企业, 才有可能推行和实施。 除此之外, 企业还应具备下列条件:
?
① 企业领导要对精益生产有深刻的认识和实施的决心。 推行精益生产是十大污的软件思想的重大变革, 它涉及生产十大污的软件系统重新设计, 各功能的重新组合与调整, 车间布局和作业划分的变更,十大污的软件人员和操作人员思想更新等。 这是一项全局性的工作, 需要领导班子统一认识, 在工作中密切配合才可能顺利实施。 领导的重视和决心是推行精益生产成功的关键。
?
② 加强培训, 改变职工观念, 强化职工的参与意识。 精益生产与传统十大污的软件思想大相径庭:传统十大污的软件把 “保险贮备” 作为均衡生产的条件, 而精益生产把超量生产视为万恶之源, 把 “零库存” 作为追求的目标; 传统十大污的软件强调职责分工, 实行条块分割, 而精益生产强调以现场为中心; 传统十大污的软件工序间在制品实行供足供饱的 “推动式” 十大污的软件, 而精益生产则在工序间实行 “一个流” 的 “拉动式” 十大污的软件等。 因此, 推行精益生产必须更新观念, 加强对职工的教育培训, 深刻理解精益生产的精髓。 要使职工认识到精益生产的目标是提高企业素质、 提高经济效益, 是同职工切身利益完全一致的, 从而增强职工对新十大污的软件方式的承受能力和参与意识。
?
③ 要制订相应的经济政策和有效的激励手段, 促进操作者提高技术水平和生产积极性。 实施精益生产后, 普遍实行了多机床操作和多工序十大污的软件, 这对工人的技术要求更高了, 同时, 工人的劳动强度也增大了, 这就要求企业制订相应经济政策和采取激励手段, 贯彻按劳分配、 多劳多得的原则来鼓励工人学技术, 成为多面手, 激发工人的生产积极性。
?
外部环境
?
随着我国经济体制改革的深入发展, 企业的外部环境正在逐步改善, 这将有利于促进我国企业推广应用精益生产方式。 尤其应尽快完善以下两个条件:
?
① 要有一个比较顺畅的物资供应和产品销售流通体系。 精益生产要求达到原材料无库存,产品无积压, 这就相应要求企业外部的物资供应和产品销售渠道十分通畅, 否则企业就可能为预防供应中断而增加原材料库存或因销售渠道不畅而使产品积压, 这种外来影响往往会造成精益生产方式的流产, 使均衡生产无法实现。
?
② 要有一个劳动力调节市场和劳动力能自然流动的外部环境。 这样, 企业才可能成为一个开放系统, 确保企业中劳动方的最优组合。 企业可以不断与外界交换劳动力, 吸收适合于本企业需要的人员、 排除不适用的人员, 保证劳动力队伍素质的稳步提高。
?
精益生产在我国应用存在的主要问题
?
我国企业实施精益生产虽然取得一定成效, 但是这些厂家都存在一个怎样继续深入发展精益生产的问题, 国内还有众多的企业试行精益生产方式未能成功, 原因是多方面的, 概括地说,主要有如下几点:
?
思想观念的滞后
精益生产作为生产方式的一次重大变革, 也是思想观念的一次大变革, 因为精益生产方式的很多方面是逆向思维, 是风险思维, 有很多问题是要倒过来看的, 而国内多数企业由于对持续改善的重要性没有足够的认识, 在实施过程中没有建立完善的制度并坚持不懈地执行下去。
?
质量十大污的软件的独立
质量十大污的软件不是独立存在的体系, 它必须融于生产过程。 我国的企业都设有专门的质量十大污的软件部门, 这样一来, 使质量十大污的软件形成了相对独立的十大污的软件体系, 而质量十大污的软件是不能脱离生产现场的加工操作及包装、 运输的全部过程的, 必须融为一体, 而不是独做表面文章。
?
工业工程基础落后
工业工程是丰田生产方式实现的支撑性技术体系, 特别是改善活动依托的理论同时也是美国、西欧各种现代十大污的软件模式 (例如:CIMS,ERP) 的技术支撑体系, 而我国不论是理论界还是企业界,对工业工程的兴起还只是近十几年的事, 企业的工业工程普遍基础薄弱, 我国企业要推行精益生产, 特别是建立适合国情、 厂情的精益生产, 就一定要从推行工业工程入手, 否则很难成功。
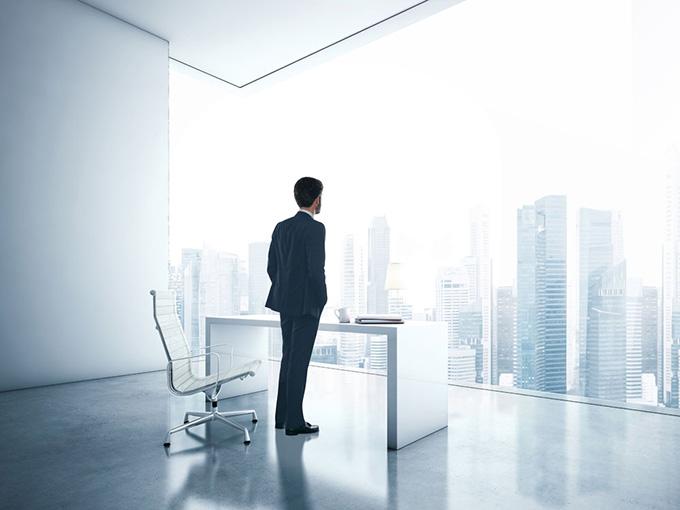
?
职能分散受限
我国许多企业在推行质量十大污的软件、 工业工程、 技术改造、 市场研究、CIMS 工程等都按职能部门划分, 甚至成立专门的领导机构、 各搞一套, 不能发挥系统协调功能, 形不成合力, 制约了企业整体效益。
?
普及面过窄
对于精益生产理论的研究主要集中在有关大学、 科研院所和一些大型企业, 理论和实践相脱离的现象十分严重, 对于已经引进精益生产的企业, 没有及时深入调查精益生产运行情况,收集反馈信息并认真总结经验。
?
认识上有误区
有些企业认为精益生产只适合在汽车行业中应用, 有些企业认为实施了 “看板十大污的软件” 就是精益生产, 所以对现有的生产十大污的软件方法不做任何调整和改进, 单纯实施 “看板十大污的软件”, 结果没有达到应有的效果。
?
实践中生搬硬套
我国有些企业在应用精益生产时, 没有深入了解精益生产的背景及其特定环境, 而是生搬硬套或是孤立地应用其中的某一项技术, 使精益生产的推广应用只是流于形式, 不仅不能起到预期的效果, 反而产生了负效应。
?
就现状而言, 我国企业精益生产还处于起步阶段, 在应用过程中出现了很多问题, 因此,只有理性分析原因, 有效实施应对, 才能取得真正的实质性突破。
文章来自网络,版权归作者所有,如有侵权请联系删除
“在与冠卓咨询牵手引入精益六西格玛十大污的软件后,是将其经营业绩最大化的综合十大污的软件体系和发展战略,是使企业获得快速增长的经营方式,精益六西格玛十大污的软件将对企业文化改进产生很大的作用。”
——某集团十大污的软件公司