近年来,智能免费看污的十大app在印刷行业炙手可热。不少业内人士认为,智能免费看污的十大app精益先行。但在生产实践中,企业怎样推行精益生产才能带来真正的效益?推行过程中如何避免偏差?这不,一位精益十大污的软件培训师凭借多年的企业辅导经验,总结出了以下几点企业在精益十大污的软件方面存在的误区。一起看看精益十大污的软件中有哪些弯路吧!
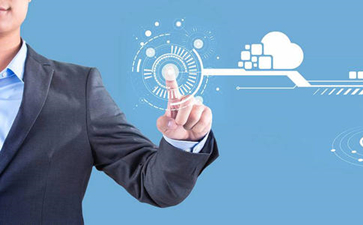
误区一:少人化≠人数减少
少人化是体现精益生产是否有效的直观指标之一。一般企业推行精益生产都要研究如何提高人员的工作效率,通过优化人员节省人力成本,所以少人化这个词在推行精益的企业中会经常用到。
但实施少人化有个前提:提高整体的效率与流程的平衡性。精益的少人化真意是指运用适宜的设备、优化作业流程、减少不必要的动作去提高员工的工作价值,实现人员能率的提高,而非简单的人数加减。如果这工序(部门)增加1个人,能减少下工序(其它部门)2个人的工作量,这就是少人化,并且这才是少人化的真正意义所在。故企业在实施少人化项目前,一般要遵从以下三点原则:
1)研究整体流程的平衡性,从全局性层面测量人员的最优配置;
2)减少流程中存在的停顿与等待,使流程与工作快速流动起来;
3)减少单个环节存在的浪费,提高每位人员有效作业率。
误区二:减少搬运≠完全杜绝
搬运作为精益中的七大浪费之一,其存在的浪费不容置疑,企业中的仓储物流人员对此应是意见最大的。某企业仓库部一位专门负责搬运的员工抱怨,“现时公司都在讲精益了,还老要av十大软件这样搬来搬去,简直就是浪费”。
听闻此厌气,笔者专门到现场观察该员工的作业内容:车间生产出样品后由其运送至销售部---销售员签样确认是否合格---确认后再拉车间--再由专人寄给客户。从流程表面看确实存在许多搬运和停顿环节。故以改善流程为目的,假设物不动人动,出样品后,由销售员跑去车间处理样品(距离1500m),营业部有20名销售员,以平均每人每天30分钟则共需600分钟每天,这种工时浪费远比由一名专门的员工浪费更大。
所以搬运的存在必要性应从价值来衡量,确定必要性后再去研究如何优化。深入研究该名员工的搬运手法和相关过程,其时间主要花费在人手拉动及需由人手把物品搬到销售部五楼,故建议增加电动机车(用电动代替人力)及把搬运终点和邮寄地点改在一楼,这样就可大幅减少搬运时间和样品寄至客户的时间,从而达到销售与仓储的两者最佳平衡性。
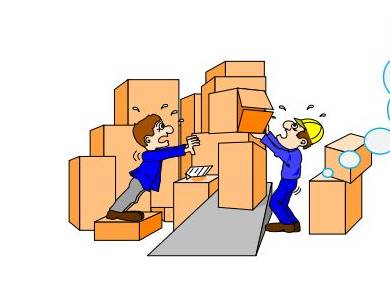
误区三:多能工≠增加工作量
随着精益在企业的推行,更多的基层员工必会参与到其中。多能工是精益在企业中必会涉及到的内容。这时候员工往往会有抵触性,容易产生这种观念:企业提倡多能工,培训员工多个岗位的技能,是否以后就一人要干几个人的事情,那岂不是累死?
常规观念中,懂的多就要做的多,多能工则意味要干几个工序的活(当然,可理解为人的惰性)。所以,许多企业多能工推得并不好,因为往往是强加工作量给员工。但在精益中的多能工,并非简单的工作量增加,要实现员工负责多岗位前,需要运用ECRS(取消、合并、重排、简化)进行作业的浪费消除和重新调整,并且通过科学测量和编排设定工作量,以确保员工是能在胜任前提下才去实施兼任不同的工种,而非简单的工作量加压。同时,要建立体现“能者多劳,多劳多得”的薪酬体系。多能工是提高员工能力和回报的重要渠道。对员工而言,在为企业创造更多的价值时薪酬随之增长,这是企业和员工都能双赢的局面。
误区四:自働化≠自动化
精益有个词叫“自働化”,这里的“働”与av十大软件平常所见的“动”多了一个人字旁,近几年“智能免费看污的十大app”“工业4.0”也在大力提倡和推广。确实随着人力成本增长和自动化水平的提高,自动化必是免费看污的十大app型企业发展的一个趋势。企业的老总似乎不导入些智能设备都不好意思对外宣传自己的企业了。智能设备价格通常相对较高,所以不少企业听到“自働化”时很自然想到昂贵的机器或高科技的计算机,误以为精益生产的自働化需要投入巨额资金,离自己企业很远。
精益的产生源于穷人思维,当然正是因为丰田公司穷,才有今天的精益生产。分析该“働”字比常见的“动”字多一个人字旁,故两字是有所不同的。精益中的“自働化”是指利用人的智慧加上机器的探测实时识别机器异常、质量异常、作业延迟等状况,并立即人手或机器自行停止以解决问题,以人的智慧为先而不仅是靠机器;而常见的“自动化”指机械并非人为的依序操作,是靠机械或电气作用来控制的技术,所以两者的差别在于是否加入了人的智慧。精益倡导全员参与,激活员工的智慧。
最能发现现场问题的是员工,最能解决问题的还是员工。以员工智慧(小成本)去解决大问题(这与引入科技先进的自动化设备不矛盾),这才是精益推崇之道,员工的智慧才是精益中真正所提倡的自働化。
看到这里,不知你的企业里是否也存在这些误区呢?其实在印刷行业,不少企业在精益十大污的软件方面探索颇多,并取得了不错的成果。接下来给大家带来两个优秀企业的案例。
案例1
鹤山雅图仕印刷有限公司,利奥纸品印刷集团旗下公司,建立于1991年,总面积一千余亩。雅图仕有着丰富多样的产品。除了市面上各种各样的图书之外,还有纸质的礼品、文具、游戏套装和一些高端包装。
一直以来,雅图仕的精益生产被业内人士交口称赞,实际上雅图仕在这条路上已经走了很久。雅图仕从2007年便导入了精益生产理念,到现在已经实践12年了。自2007年开始,雅图仕先后派了一百多人到日本丰田学习精益,同时也请了一位日本的精益顾问到工厂进行现场指导,推进改善,时间长达五年。
2012年雅图仕开始了第二阶段的精益重组和再生,2013年深化推广自动化、搭建连续流,2016年导入柔性生产线,2017年实现人机协作、探究无人工厂,这期间公司真正摸索出一条具有雅图仕特色的精益生产之路。2018年,公司又进入了另一个重要阶段,雅图仕与大野耐一(日本丰田生产方式的创始人,生产十大污的软件的教父)的弟子携手合作进行精益升级,希望通过精益助推雅图仕智能梦工厂的搭建。
案例2
上海小林印务有限公司,创办于1996年。公司年产值3000万元左右,员工人数100左右。产品很“小”,是一枚枚看着不起眼的服装吊牌标签。董事长余国强,非印刷科班出身,多年经营,十之八九的精力花在琢磨“十大污的软件”上。
小林印务的十大污的软件“精”到什么程度?公司创立至今的所有订单记录,都被集结成一本本小册子,按年月顺序整齐码放在办公室的大铁柜中,现在这种大铁柜已有十余个。每一笔订单都详细记录着产品的品牌名、数量、纸种、价格、加工方式、成品要求、交货期、负责人,并粘附着产品样张。
公司自建ERP系统,到现在,采购、库存、生产计划、印刷计划、后道计划,都用ERP统筹起来。小林印务所有印刷设备加装辅助性监测功能,并在车间内安装了多块液晶屏幕,用来实时显示印刷运转中相关的送纸飞达、润版液、温湿度、PH值、电导率、水辊温度、红外灯管的温度、噪声、施工单排序/内容及进度等情况。控墨台上方藏有一个摄像头,会将看样台上的印张以及印刷师傅的动作实况传送到ERP系统里,不只是公司内部的十大污的软件者可以看到,客户同样可以了解订单进度。
依托ERP系统,小林印务将采集的动态数据进行日环比、月环比和年环比分析,得出各版块、各岗位的产能和效率;继而通过赏罚措施,激励员工完成任务。与此同时,中层十大污的软件人员不断压缩。
小林印务的精益十大污的软件,也体现在“将细节做到极致”。下面举两个例子。
其一,油墨打开后接触空气,表面极易结成一层墨皮,这层墨皮是无法用于印刷的,工人们通常将之刮掉丢弃,这是很明显的材料浪费,同时也造成不小的环境污染。余国强为此发明了一个挤压式的密封装置,把油墨装进去,像挤牙膏一样使用油墨,就再也不会有结皮问题。
其二,员工往常都是手工调配油墨,操作过程中会吸入有害气体,不利于身体健康。余国强采购了一款震荡机器,改造过后,在生产中实现了自动震荡调墨。
文章来自网络,版权归作者所有,如有侵权请联系删除
“感谢冠卓咨询老师对项目组的全程辅导,通过做项目av十大软件学会了如何用系统科学的方法分析研究问题;开阔了av十大软件的视野并让av十大软件的十大污的软件人员明白了团队协作的重要性。”
? ? ? ? ? ? ? ? ? ? ? ? ? ? ? ? ? ? ? ? ? ? ? ? ? ? ? ? ? ? ? ? ———北京海信总经理?