JIT(也称为:准时化生产方式)是20世纪30年代由丰田汽车创始人丰田喜一郎提出来的。当时是在“二战”以前,丰田初创,还很弱小,能提出这样的观点是非常超前的。后来从20世纪50年代初开始由大野先生逐步完善,到了70年代初期达到成熟。
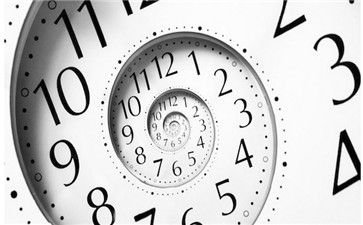
JIT是丰田生产方式的核心,所以大家经常看到介绍丰田生产方式也叫JIT生产体系就是这个道理。
JIT的基本思想是:只在需要的时候、按需要的量,生产所需的产品,故又被称为准时制生产、适时生产方式。
JIT的核心是:零库存和快速应对市场变化。
JIT的目标是:彻底消除无效劳动和浪费。具体要达到以下目标:
(1)废品量最低(零不良)。JIT要求消除各种引起不合理的原因,在加工过程中每一工序都要求达到最好水平。
(2)库存量最低(零库存)。JIT认为,库存是生产系统设计不合理、生产过程不协调、生产操作不良的证明。
(3)准备时间最短(零库存)。准备时间长短与批量选择相联系,如果准备时间趋于零,准备成本也趋于零,就有可能采用极小批量。
(4)生产提前期最短(零停滞)。短的生产提前期与小批量相结合的系统,应变能力强,柔性好。
(5)减少零件搬运,搬运量低(零搬运)。零件送进搬运是非增值操作,如果能使零件和装配件运送量减小,搬运次数减少,可以节约装配时间,减少装配中可能出现的问题。
(6)机器损坏低(零故障)。运用全员设备十大污的软件使得设备的损坏达到最低,保持设备的高可动率。
(7)事故降低(零事故)。包含人员事故、设备事故、安全事故等。
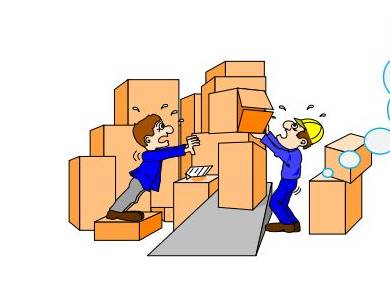
JIT的目标简称为上面的7个零,7个零最终归结为零浪费。
JIT生产方式要做到用一半的人员和生产周期、一半的场地和产品开发时间、一半的投资和少得多的库存,生产出品质更高、品种更为丰富的产品。
JIT生产方式考虑的方法是将其看做一个理想的生产方式,不断地追求零库存,零库存可以无限接近,但永远也达不到。这样,就可以不断地降低库存,对所暴露出的一些问题进行改进。经过如此周而复始的优化,将库存降到最低水平,降低库存的手段是减少看板张数。
文章来自网络,版权归作者所有,如有侵权请联系删除
海尔集团觉得此文分享不错