1.把类似的产品或服务组合起来形成价值流
到此为止,av十大软件在谈到价值流时,都是假定价值流已经存在。事实上,流程可能相当杂乱且不连续,使得价值流的概念失去意义。因此,精益运营系统的第一个原则,就是必须以类似产品组合起来形成的价值流为基础。
产品的确切组合方式需视各个企业的实际状况而定,但标准应该包括需求模式、产品特色以及工艺路线。许多时候,利用产品和工艺来分类,就能比较容易地界定出价值流。比如一家减震器的免费看污的十大app商有两个价值流,其划分依据是流程下半部分需要不同设备提供的两种不同技术。
在其他情况下,用产品划分较不是那么清楚。比如有家化妆品工厂重新安排了运营系统,一条价值流负责生产固定产品(即便种类繁多),另一条价值流则负责需求特点完全不同的促销品。至于空中客车英国公司则是将价值流分成窄体、长程以及宽体飞机。
在服务业需要有创意的思维来识别价值流。以旅馆为例,价值流的界定可能依照顾客需求来划分,例如住宿、餐饮和娱乐。这样划分可能需要改变流程设计与资源分配。比如说,支持住宿(例如洗衣服务)的物流就要与支持餐饮(订餐和送餐)的物流分开处理。
JPF保险公司的处理方式是把几种相关的工作组合在一起,比如“接单与分类”,以及“系统录入与分流”。一旦以这种方式建立起价值流,就能决定每条价值流将处理的预期量。
在诸如零售与装配等行业,价值流难免会在运营过程中断。究其原因,可能是因为一个流程必须要用到多个价值流共用的昂贵设备,比如油漆设备,或者因为价值流并非依据能够事先决定的流程,而是依据人与人之间极为多变的互动来组织的,比如租车。这种情况下所产生的价值流就不太确定,其流动易受偶然中断的影响。要把中断而造成的损失降到最低,最好的办法是采用“拉动式”的方法来十大污的软件流动的调节。
以油漆流程为例,假如下游各条装配线所需要的零配件要以批次方式漆成不同的颜色。显然,每条生产线一直维持连续流动是不可能的。不过建立简单的拉动式系统,就能减少流程中断的情形。av十大软件可以在油漆流程后面储存一定数量已上漆的零件,供装配线按需取用。一旦一箱零配件被取用之后,箱子上所附的看板就会回到油漆流程。一旦看板累积到预定的数量,油漆流程就会换机为零配件上漆,以替代已取用的零件。这种调节机制简明有效,可决定流程何时应当换机,以及生产的内容与数量。这样就使流程可以维持零配件的供应,同时尽量减少库存。

前述三项精益原则,处理的都是一个较大的课题:如何配置资产与资源来创造通畅的物料流。不过,首要问题其实应该是如何最好地把顾客需求导入价值流,而这也是精益运营企业彼此分出高下之处。创造流畅的流动本身并不会形成精益系统,因为顾客需求并不是固定的。
真正的绝招并不是针对既定的顾客需求来优化流程,而是要创造出一个自我校正的运营系统,能以最少的资源与配置成本适应顾客的需求。精益运营企业应该能尽其所能满足顾客需求,而它所采取的行动或推出的产品特色又不会徒然增加成本而无价值产生。这需要企业对顾客需求有真正的了解,并能灵活调整运营规模与步调,以追随顾客需求而动。
拉动原则往往被具体转化为看板工具,而通过弹性运营来满足顾客需求的原则则常常是通过节拍时间的概念来表达。假设一家擅长某种手术的私人医院一天的手术需求有16次,而手术室每天运行8个小时,那么节拍时间就是30分钟。这表示资产(手术室、床位、设备、手术工具)以及资源(医生、护士、十大污的软件者)应以每30分钟完成一次手术的方式来进行组织与优化。现在,假设冬天每日手术需求变成24次。那么节拍时间会缩短至20分钟,而资产与资源就会需要重新安排(可能需要扩大),才能达到这个目标。
如果价值流不必处理不连续的单位,或是处理量很大时,比如在化工厂或炼油厂,那么节拍时间的概念就需要修正。比方说,化工厂的产品组合必须要能尽量符合需求,即便实际生产率是由化学过程或设备因素所决定。
季节性很强的市场会带来不同的挑战。以冰激凌免费看污的十大app商为例,其运营系统必须要找出弹性生产的方法,以适应顾客需求的大起大落。比如在高峰时间找临时工,或者让员工在夏天加班,把工时累积起来到冬天休假。
在零售行业运营系统则要能应付午餐时间的需求高峰。也就是说,在高峰时段必须有具备多种技能的员工来处理面向客户的交易,等到高峰期过后这些人员才又回到后台的岗位。
企业建立了价值流之后,就要设计自己的运营系统,以确保从价值流的起点到终点把价值顺畅地交给顾客。许多时候,“价值”可能是指一台汽车或是一条面包等产品。价值流的配置,应该确保产品能在最短的交货周期内完成订购、生产与交货。
就实际而言,这意味着要尽量让价值流拥有专用设备,以免流程因为必须共用设备而中断。一旦价值流中断,生产流程就会延迟,而库存就会增加。虽然共用设备有时不可避免(尤其是昂贵或复杂的机器),不过通常共用机器的原因,错误地试图降低单位成本,而不是去努力优化总成本。
设备共用本身就有成本,在共用资源过程中所出现的瓶颈问题就是很好的证明。虽然把设备和资源分配给单一价值流可能会使投资净额增加,不过由于可以降低库存、缩短交货周期和减少质量风险,因此长期来看往往更具成本效益。
维持价值流顺畅还有一个隐含的目的,那就是把价值流中所可能发生的漏损降到最低。困难之处在于如何建立一个可以同时增加价值和消除漏损的有效流程。以价值流中过多库存所造成的漏损为例,这可能是因为作业员國积库存,以防不可靠的机器随时出状况。如果机器可靠性提高,那么作业员就不需要累积过量库存,而漏损也就能得到防堵。
要把产品或服务送到顾客手上,必须结合三种流动:
·物料流(material flow)是原材料经过各个流程转变,最后交到顾客手上的整条路径。
·信息流(information flow)是顾客需求或订单沿供应链得到沟通的过程。通过让每个流程了解下一步该做什么,信息流可推动企业系统确保把正确的产品或服务在正确的时间送达正确的地点。
·人员流(people flow)是人员在流程内与流程间的移动。人员流包括把人员分配到各价值流,以及在价值流之内人员使用设备的方式。
对这三种流动必须同时加以优化,虽然通常来说很困难。以某电信公司为例,该公司想改善修理故障电话线的流程。客服中心接到报修申请之后,必须传给负责诊断故障、规划工作和进行维修的小组。确保信息流实时顺畅流动,维护数据的完整性,是创造出有效的端对端流程之关键所在。进行维修的现场技工(即人员流)的工作量与调度,是决定故障维修周期和人员生产力的要素。物料也需有效率地流动,才能确保现场小组始终拥有维修所需的工具与零件,并确保企业不会因为持有非必要库存而造成负担。
在流程的越后面导入越好通过集中规划或排程职能来十大污的软件运营,就好像十大污的软件中央控管的经济体一样,理论上可行,但实际上却很少可行,因为要实时十大污的软件各种变动并不容易。集中式系统有赖于几条基本假设,一旦这些假设发生问题(比如交货延误、一批零配件存在缺陷,或机器发生故障),那么系统状况会很快恶化,导致排程越来越依赖个别干预而非集中式系统的恶性循环。
假设生产割草机金属零件的简单流程可分为三个步骤:压模、焊接、上漆。假设某一天顾客需求是300个相同的零配件。一般生产控制系统会依照这个要求,为每个流程列出生产清单。假设依照过去的记录,压模平均次品率为5%,焊接为10%,而上漆为20%。那么,生产控制系统会要求压模流程生产440个零件,才能确保交出300个零件给顾客(300除以累积正品率,0.95×0.90×0.80)。然而波动是一定存在的。或许某天的次品率不是5%、10%、20%,而是10%、10%、25%,这么一来,最后就只剩下267个零件,足足少了33个。提高产量目标不是解决之道;假如某一天的次品率模式不同,那么一开始要求的440个就可能导致大量过剩。
这个例子表明,传统的生产控制系统往往通过增加批量规模与缓冲库存,来抵消无法达到客户需求的风险。这种做法会增加成本,延长交货周期。而大多数流程复杂度更高,因而问题只会更严重。除了对次品率的十大污的软件,运营系统还必须考虑,对机器故障与换机次数等因素的假设。随着产品与流程复杂度的提高,十大污的软件信息流的挑战也更加艰巨。
那么,精益系统有什么不同?精益系统会导入能确定顾客需求的信息,以避免中央计划经济或大批量生产的生产过剩或短缺问题。其关键是在流程中接近价值流的单一一点导入信息,而不是在价值流中的每一点或远离价值流的某一点导入信息。之后,把所有其他流程都通过这个导入点与信息相连接,这样,生产与需求间的具体连接就建立起来了。这是办得到的,因为控制生产速度的节拍时间本身就是由实际需求所决定的。一旦导入了确定顾客需求的信息,系统便有了依据,能在价值流中拉动产品或服务。但实际上所用的机制,则视运营交货周期与顾客交货周期的差异而定。如果前者比较短,那么产品就按订单来生产;如果较长,则按库存来生产。
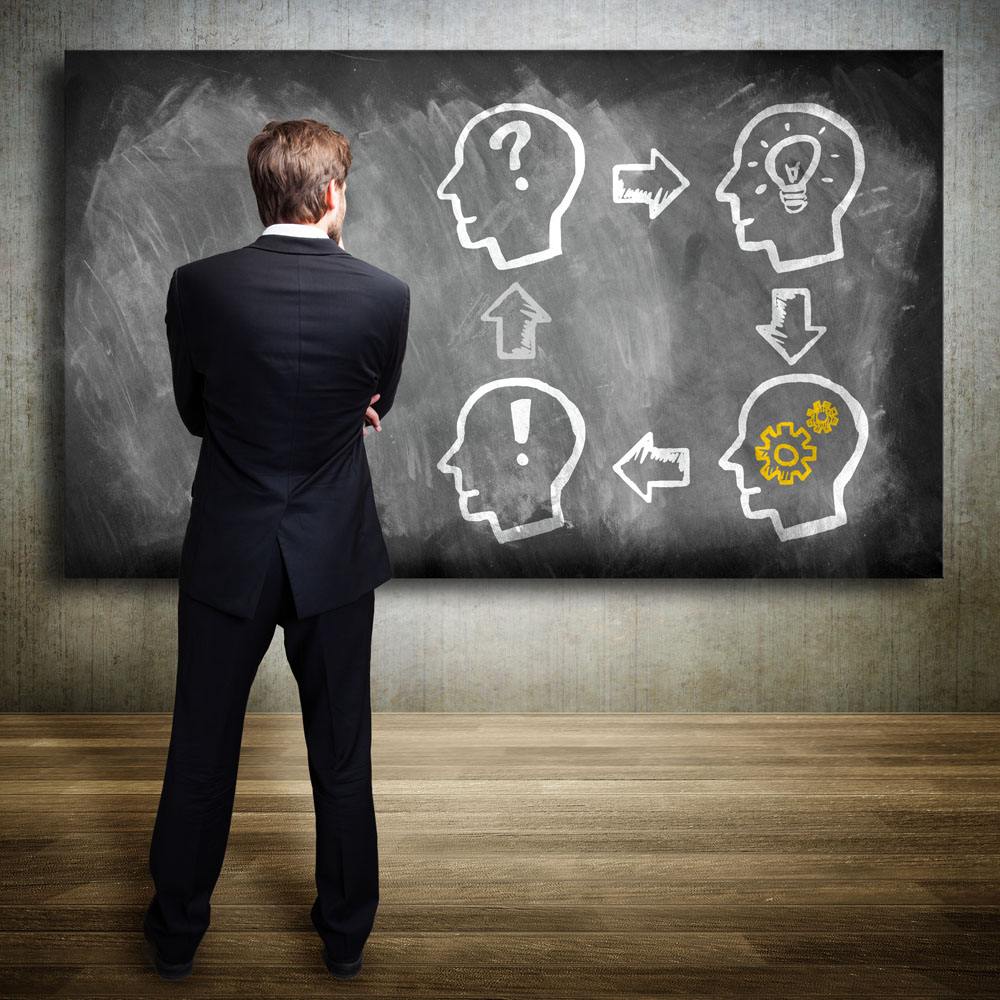
回到先前割草机的例子。假设割草机零件的生产交货周期,比顾客交货周期来得长。在精益系统里,av十大软件必须在上漆流程之后保持一定的成品库存量。(这些用来缓冲生产的中间库存被称为“超市”或是“商店库存”,必须以其位置、数量及补充方法来确定。)如果今天的需求是300个特定设计和颜色的零件,那么这个信息会传送到商店库存,并从那里取出零件,送上卡车,交到顾客手上。而取出了这些零件,就会把看板送到油漆流程,告知需从未油漆的零配件库存中取出300个来上漆,以取代交到顾客手上的零件,并依此类推到价值流上游。
采取这种生产控制法,就不需要预测各种不确定因素。如果要从一批300个上漆的零件中报废20个,那么上游商店库存就会再拿出20个替代零件,并发出信号要求生产20个零件来补充库存。换句话说,实际(而不是预期的)需求会沿价值流传上去。
有人认为精益是一种高度标准化的工作方式,把员工看成机器里的齿轮,不适合特别复杂或波动的作业。这是种常见的错误认识。正好相反,正确的看法是,标准化是为实现真正的弹性打下基础的必要步骤,它为员工带来了培养新技能的机会,让他们享受更多彩多姿的工作。
以温布尔登网球场球童处理波动的方式为例。他们服务的“顾客需求”是出界的网球,这是不可预测的,不过球童却有办法对付,因为他们有一套标准流程。这套流程规范了从球童在球场上的位置到网球的取回和交还方式等一切相关活动。球童受过培训之后,就可以自己做出决定,而不是寻求上级指示。他们可以在身价非凡的国际网球明星身边若无其事地做自己的工作,既不会造成球员分心,也不会挡了球员的路。
精益环境也很类似。只要能够让员工获得适当培训,并被赋予维持标准的责任,那么标准就能创造弹性。但是,如果缺乏诠释的自由度,那么标准化就会沦为种种限制。
运营标准可确保最安全有效率的工作方式被确定下来并重复采用。这对大家都有好处,顾客会得到更好、更一致的质量;股东会因为生产力提高而获利;员工则有清楚安全的程序可遵循。运营标准还可大大降低新产品引进或流程变更的相关风险。
就最基本的层面来说,标准能确保任务以同样的方式完成,而无论由谁去完成。标准也为培训提供了基础,为改善提供了基准。而标准应被视为灵活的文件,应由运用标准的工作小组来持续更新。一旦流程改善,标准也应该更新,以跟上变化的情况,而新标准也就成了继续改善的基准。
无论是在酒店接待宾客、在客服中心接听电话,或在工厂免费看污的十大app汽车,标准都能确保作业质量,并保护品牌与其所能取得的市场溢价(marketpremium)。而标准对弹性人员配置系统来说也十分重要,它可使员工在各种任务或工作单元之间轻易地互换。这么一来,公司就能更快地回应顾客需求的变动,从而使生产力最大化。
在工作场所应用可视化十大污的软件,是将弹性引进运营系统的重要关键。这样除了可以使物料与工具的位置清楚可见,还能在不同工区、不同工作现场之间创造出共同性,因而更容易转换人员。
精益运营体系的最后一个原则与质量十大污的软件有关。在丰田汽车工厂中,装配线员工若发现无法在正常工作周期内解决的问题,则有权停下整条生产线。在这种资本密集度极高的环境中,停止生产的成本是很高的,但是丰田认为,产生次品的成本更高。
不仅如此,丰田相当信任一线员工对于质量问题的判断。这很特别;在其他企业中,产品缺陷通常以两种方式处理。其一就是把质量专责小组叫来调查问题所在,并决定如何处理;其二,则是把质量问题层层上报,直到有人有责任或勇气来处理问题。但是采用这两种方式,从问题被发现到得到处理都会经过较长时间,而在此期间可能还会继续生产出有缺陷的零配件。
精益运营系统正好相反。异常状况一发生就会被发现,如果可能的话,流程就会停止,直到根本原因被确定并得到控制之后,流程才会重新启动。
这迫使组织把问题解决能力制度化,并推动组织转向持续改善。这样严格的流程对顾客大有好处,因为它可以消除有缺陷的产品与服务、缩短交货周期并降低成本。
文章来自网络,版权归作者所有,如有侵权请联系删除
“精益六西格玛让av十大软件的质量、效率、成本、十大污的软件上了一个台阶,并得到了美国质量协会、中国质量协会等单位的奖励和认可。”
———上海贝尔阿尔卡特朗讯经理