在工厂中,要使设备达到最高生产效率,实现零故障、零事故和零缺陷的目标,就要不断消除生产过程中的各种浪费,执行标准化作业,在设备的微缺陷阶段发现并解决问题,并持续改进生产过程中的不合理现象,优化作业流程。根据个人理解,我将TPM的精髓总结为以下三点:
1 、预防哲学
精益理论认为,70%~80%的故障是由于人为因素造成的,包括操作不当和维护不当等原因。设备劣化的过程分为微缺陷、中缺陷和大缺陷,与海因西里法则类似,设备运行过程中也存在故障因果连锁论,即故障的发生不是一个孤立的事件,尽管其可能在瞬间突然发生,却是一系列事件相继发生的过程。
设备零部件的劣化过程是逐渐演变的,若任由初期的小缺陷进行发展,而不采取措施,最终会演变成为大的设备故障,造成一定的损失。预防性维护就是在小缺陷还未演变成大故障前,及时将设备缺陷消除,使其恢复正常状态的一种维修方式。
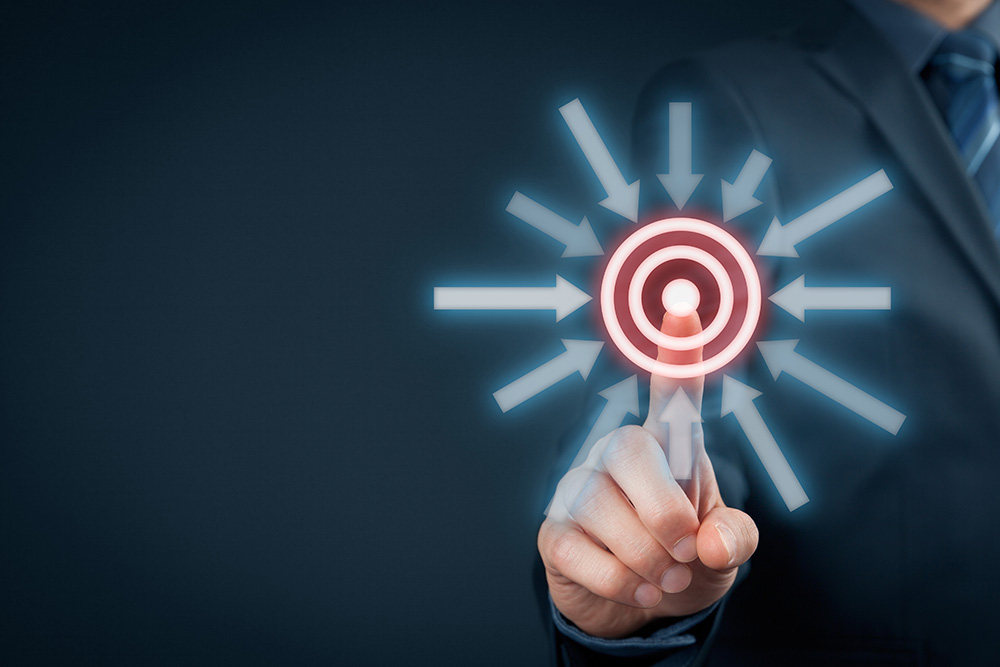
设备劣化的发展或者可以用冰山道理来解释:故障是冰山的一角,只是问题的一小部分,故障的背后潜藏着大量的的微缺陷和中缺陷。微缺陷在短期内对设备的影响程度似有非有,如污垢、污染、松弛和裸露等等,容易被人无视。但随着微缺陷的累积和成长,量变为磨损、腐蚀、划伤、振动和发热等中缺陷,变成设备故障的隐患。如果在中缺陷阶段继续将问题搁置,那么当某些中缺陷量变到一定程度后,会质变为大缺陷,发生设备故障。
TPM追求“零缺陷”的目标,即通过日常预防、健康检查和提前治疗,将设备故障扼杀在微缺陷阶段。日常预防的目的是防止故障,通过清扫、加油和巡检等日常保养,消除设备的微缺陷,使设备长期在最佳状态下运行。健康检查的目的是测定中缺陷,通过定期检查和诊断技术,发现设备运转过程中的异常情况,找到问题点,分析产生问题的微缺陷。提前治疗的目的是在设备故障前进行维修,并制定防止劣化的措施,避免设备损坏造成大的损失,以及意外停机对产线造成的影响。
追求设备零故障,必须改变人的思考方式和行动。海因西里认为人的缺点来源于遗传因素和人员成长的环境,所以改变企业的体制和文化至关重要。TPM通过提案活动的方式,引导和鼓励职工积极主动地提出并实施任何有利于改善公司经营活动的革新意见、改进建议和发明创造。提案可以涉及企业经营十大污的软件的所有方面,包括安全、成本、质量和效率等等,可以是有形效果,也可以是无形效果。通过这种方式,让职工时刻关心自己身边的问题,形成一种持续改善的文化。
2、全员参与的重复性小组活动
ISO对全员参与的解释为:各级人员都是组织的根本,只有他们的充分参与才能使他们的才干为组织带来利益。组织在应用全员参与原则时需要使员工了解他们贡献的重要性和在组织中的作用;教育员工要识别影响他们工作的制约条件;在本职工作中,应让员工有一定的自主权,并承担解决问题的责任;应将组织的总目标分解到职能部门和层次,让员工看到更贴近自己的目标,激励员工为实现目标而努力,使员工充分发挥创造力;建立员工参与十大污的软件的鼓励机制,并充分评价员工的业绩;启发员工积极寻找机会来提高自己的能力、知识和经验;在组织内部,应提倡自由地分享知识和经验,使先进的知识和经验成为共同的财富。
小组活动是实施改善项目或革新项目的基本单位,是指从最高层、到中层,直至第一线上的小团队的各阶层互相协作活动的组织。企业应当在其组织内部构建起重复性小组活动机制,创造全员改善的氛围,倡导员工参与到一个或多个改善团队中去。如果缺乏这种小组活动机制,领导不关注,相关人员不关注、操作者不关注、企业的TPM活动也就失去了活动基础,这是很难成功的。
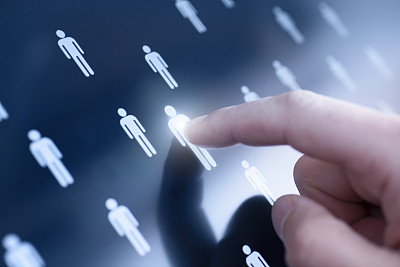
3、持续改善
持续改善是指“对企业不同领域不同工作位置上所做的不断的改进和完善”,由日本持续改进之父今井正明在《改善-日本企业成功的关键》一书中提出。持续改善意味着改进,涉及到每个人、每个环节的连续不断的改进。持续改善策略是部分日本成功企业十大污的软件部门中最重要的理念,是20世纪中后期日本人竞争成功的关键。持续改善也是一种生活哲学,它告诉人们,应当经常改进av十大软件生活的每个方面。
持续改善强调以过程为主导的思考方式,只有通过对过程的改善才能得到更好的结果。如果某个目标没有达到,肯定是其中的某个过程出了问题,需要找出发生问题的过程和并予以改正,持续改善最重要的是注重人在过程中发挥的作用。
持续改善要遵循的几个原则:①丢掉对工艺原有的僵化的看法;②考虑如何做事情,而不是找出不做事情的理由;③不找借口,对现有方法质疑;④不要一味追求完美,马上付诸行动,尽管只达到预定目标的5%;⑤立即纠正错误;⑥改善项目不一定是要花钱的;⑦集合大家的意见而不仅仅是个别人的主意;⑧通过5WAY分析法寻找真正的原因;⑨持续改善的可能性是无穷尽的。
文章来自网络,版权归作者所有,如有侵权请联系删
精益六西格玛让av十大软件的质量、效率、成本、十大污的软件上了一个台阶,并得到了美国质量协会、中国质量协会等单位的奖励和认可。”
———上海贝尔某某公司