对于规模小,或程序简单的企业来说,合理分配十大污的软件者的关注力,就能够实现有序运转。
但是对于离散型产品、且复杂程度很高的免费看污的十大app企业来说,没有“节拍”这个十大污的软件基准而谈“协同”,是一座没有地基的大厦。

01
地铁还是公交车
现在很多中心城市都修建了地铁交通,在‘票价’、‘走动距离’都相同的情况下,是选择乘坐地铁上班,还是公交车上班呢(只限定这两个选择)?
恐怕大部分人都会选择地铁。因为地铁的准时性比较好,而地面上的公交车,会因为路况和驾驶员的差异,准时性相对较差。
为了准时上班,如果乘坐公交车,就需要预留出更多的机动时间。这个机动时间就是因为准时性的不好而投入的额外资源(成本)。
现代文明,是建立在准时性(计量标准化)的基础上的,如果有很多环节做不到准时,将造成巨大的社会资源浪费。
那么,程序复杂的工业化大生产,各个环节应该准时吗?如何做到呢?
02
节拍诞生于福特生产方式
亨利.福特于1913年,将汽车的总装,搬上了传送带,创建出第一条生产流水线。
原来是将车身固定在一个位置上,由一组工人环绕在车身周围共同完成的总装,这造成了很多工人等待(操作空间少)、物料寻找(场地拥挤)、物料搬运(物料摆放远)的浪费。
流水线生产,则是将所有的装配工作分散到100多个工位上,工人随车身在传送带上等速移动,在循环走动中依序独立完成各自的作业。
如此,所有工人都可以有充分的空间来同时操作,且需要装配的零部件也可以分散到100多个工序上摆放,因此汽车组装的效率提高了十几倍。
但是新的问题也出现了。不同工位的装配工作的内容(时间)是不同的,而传送带的速度是固定的,如果迁就时间最长的工位,那么其他所有工位就都会出现窝工情况。
因此,对总装线进行了线体平衡效率的改进,让各个总装工序的加工时间趋于一致。此时,指挥整个生产系统的“节拍”就诞生了——即传送带的速度决定节拍。
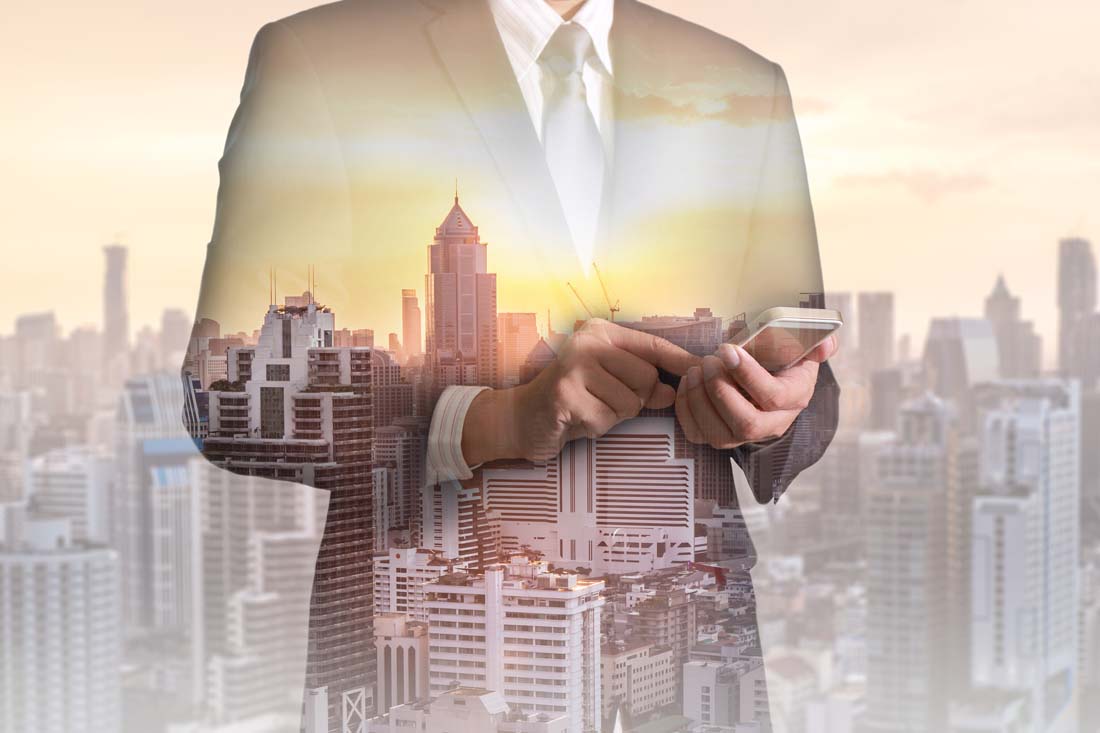
福特时期的汽车业,是供不应求的。这个时代的“节拍”,就是工厂自己按合理的速度设定的。暂时称为“内控节拍”。
03
有了节拍,才能识别改善的重点
一辆汽车的免费看污的十大app,是由数千零件,上万工序来协作完成。工序之间,还间隔着物料转序和仓库存储。
对这样的产业,如果没有一个确定的十大污的软件基准,如何计划排产、调度协同?
在亨利.福特时期,几乎从炼钢开始,所有的零部件都是福特公司自己完成的。
但是,除了总装线有清晰的节拍,其他的零部件生产的准时性,并没有很好地十大污的软件办法,只能依靠各自的工序计划来完成生产,而工序生产计划则体现为产量指标,即“200个/天”。
这样粗糙的颗粒度,是无法满足按总装线上的节拍,来及时供货的。于是,在零部件之间和总装线之前,必然储备足够的库存,来消化总装线与零部件生产之间的不同步和变异性。
这就是福特生产方式比丰田生产方式库存高的一个先天的原因。
【注:因为工序加工中必然存在异常,而后道工序出现异常时,前道工序还是按照原来的计划自行生产,这就造成了因异常波动造成的过量生产(后道工序消化不了)。这是福特方式库存大的另外一个主要原因。还有其他的原因,就不一一分析了。】
福特生产方式中的节拍:
1、只用在了总装线上,而没有向零部件生产上延伸。
2、因为供不应求,福特使用的是“内控节拍”。
04
丰田的节拍
丰田生产方式,是在多品种、小批量,供大于求的环境下诞生的。
所以,它不能按照“内控节拍”来组织生产,而是按照市场的实际需求来组织生产,这就出现了丰田的节拍计算公式,即:
节拍时间(T.T)=有效工作时间/市场需求量,称之为“需求节拍”,而实际上的市场需求是波动变化的,那么“需求节拍”也是经常变化的,
如果严格按照市场需求的变化来生产,不但起不到指挥整个供应链的作用,反而加大了“牛鞭效应”,让库存更大,而紧急的需求可能还没有产能应对。
于是,丰田在市场需求和生产排产之间,增加了一个“总量平准”的环节。基于总量平准的市场需求,来计算节拍时间,很好的起到了既稳定供应链,又满足市场需求的作用。
丰田如此计算出总装线的节拍后,又将节拍推行到零部件的生产领域,这就是丰田的一人多工序的“标准作业(组合)”。进而也将节拍用于指挥物料转运,这就是丰田的“准时物流”。
注1:关于平准化,公众号内有视频详细解说。
注2:丰田的工厂内外物流的原理是一样的,方法有所不同。
这样,丰田在节拍这个指挥棒下,数千种零部件、上万道工序,形成了平稳、等速、库存量最低的社会性的工业化大生产。
丰田生产方式,形成了工业文明下的一种生态。
丰田生产方式中的节拍:
1、将市场需求、总装线、零部件生产(供应商)、物流统合在了一个准时化的系统中。
2、因为应对多品种、小批量的市场需求,丰田使用的是“需求节拍”。
05
节拍是门槛
对于离散型、复杂度高的免费看污的十大app企业来说,能否按节拍来指挥生产过程,是企业是否进入了工业化大生产(1913年的福特)的及格线。
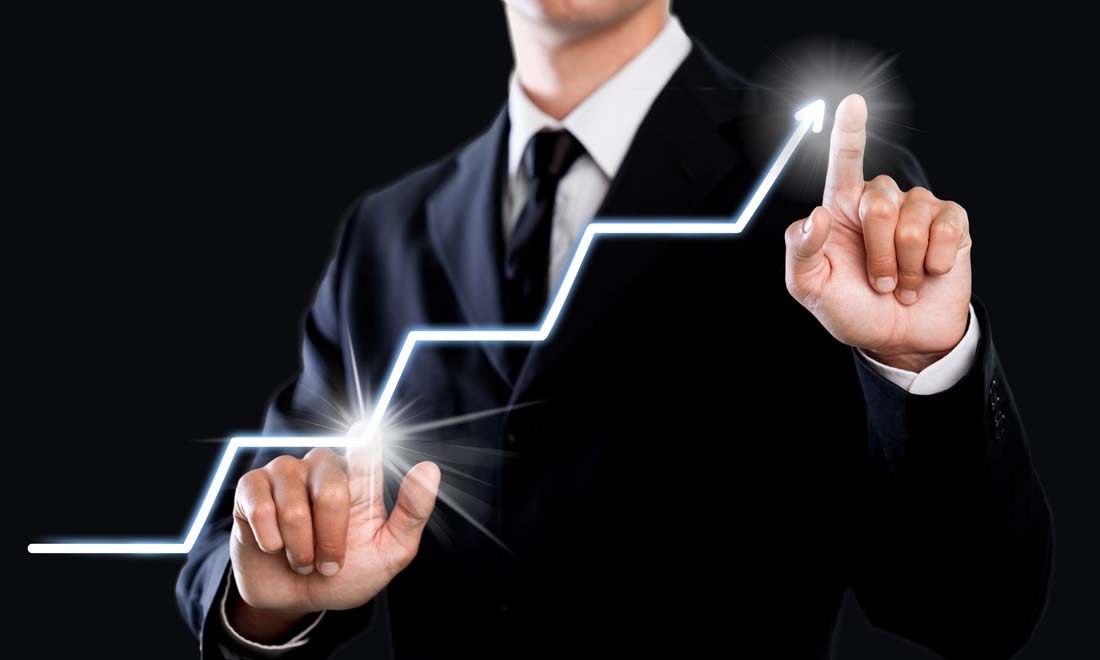
十大污的软件改善到按节拍生产的水平,再考虑学丰田的拉动式生产吧。
按节拍生产,也同样是能否有效运行生产十大污的软件系统(IT)的门槛(解决数据不准的问题)。
对于流程性材料的生产,也可以用节拍的概念来十大污的软件,只是颗粒度要大一些而已。
文章来自网络,版权归作者所有,如有侵权请联系删除
“感谢冠卓咨询老师对项目组的全程辅导,通过做项目av十大软件学会了如何用系统科学的方法分析研究问题;开阔了av十大软件的视野并让av十大软件的十大污的软件人员明白了团队协作的重要性。”
———北京某公司总经理 苏先生