01
每一个产品/服务都必须按照设计的路线来实现
毋庸置疑,但凡有点节操的免费看污的十大app企业的生产流程都是或多或少经过设计的。
但是首先,有多少公司能做到“每一个”?
av十大软件通常倾向于把“差别不大”的产品、制程按统一的方法和要求来进行十大污的软件,认为这样可以有效的合并资源并节省成本,其实更多的只是替自己的懒惰找借口而已。
差别不大也是差别,而正是貌似不大的差别才会导致质量,效率和成本的黑洞,也应该是管控的重点。
我曾经在一家公司里遭遇过这种情况。
当时的场景是在装配车间,车间有10条以上的装配线。产品名录上有上千种产品。
产品可以在任意一条生产线上进行组装。产线上的设备可以随意挪动。人员在产线上可以随意调配。
此为背景。
某日我曾就此跟各位主管生产,营运的头头脑脑探讨,建议对每个产品的生产过程都进行标准化,首先就是将哪条生产线固化到具体的生产线,然后再将各类过程参数(5M1E)固化,然后……
然后就是话没有说完,就被人打断了,妄下断语——“这是不可能的”。
当时众人同仇敌忾,一致对外的眼神让我不由自主想起了达尔文改造原始部落失败的故事。悲哀竟然如此相通。
反对的理由也很奇怪,竟然是认为这样会没有足够的生产线来生产足够类型的产品。

这些人应该都是义务教育的漏网之鱼,要送回小学的语文课堂上回炉再造。
这里的说的是每一个产品都必须按照设计的路线来实现。
又不是说每一条生产线只能生产某一单一的产品。
竖子不足与谋。
事实上,丰田模式下的每条生产线都能适用很多产品,并通常比其竞争对手要多很多。
只是,每个产品在这个路径上的都是经过精心设计和规划的。我本人就曾经将4条产品线整合到一条生产线上进行生产。
当然,至于具体是一条生产线好还是多条生产线好呢?这个没有标准答案,完全看具体情况。
其实,产品的实现路径是需要设计的。那怎样才能算一个合乎要求的过程设计呢?
简单点说,产品实现过程所需的5M1E,各工序之间的实物流和信息流都得到详细而具体的规定,在理解和实施层面都不能有任何困惑和歧义。
何为具体?
流程一定要对应到具体且唯一的流程代号。
机台要对应到明确的机台编号。
人员对应到指定的操作人员。
物料要对应到明确的物料编号。
操作方法清晰命了,如原则1规定。
……
过程设计应当如工程图纸般精确,完备。当然,如果你的工程图纸也是马马虎虎,语焉不详,当我这句话没有说过。
另外一点是,既然是设计,必然需要经过评审和验证,而不是闭门造车,一蹴而就。
唯有这样,你的过程设计不是草草而就的无脑之作。
这一点,可以参考相关的质量十大污的软件中关于过程开发和控制的要求。PDCA,并不只是一个质量的十大污的软件循环。
02
不能有分叉
这个其实比较容易理解。
迷路不是因为无路可走,而是因为岔路太多。
生产过程中也是如此,可能的选项越多,需要控制的因素就会增多,难度也会增加。还会增加思考和选择的成本。
拳击手训练中的一个的重点是本能反应,即在没有思考的状态下的攻击和躲避速度。
而对于生产工人来说,也是他们在不假思索时的生产效率最高。一定程度上来说,这也是标准化作业为什么能提高效率的原因。
因而在TPS中,每个产品只能有唯一的产品实现路线(当然,很有可能不同的产品是按相同的路线实现的)。
操作工人在工作中是没有可能去做选择题的,这个选择在过程设计时已经做了。
这个原则跟传统的关于生产线和资源利用的智慧(理念)相矛盾。甚至跟大部分人关于丰田生产系统如何工作的想法相矛盾。
在传统的见解里,产品或服务应由接下来有空闲的人员或机器来进一步处理。而不是指定的人员或机器。这样虽然人员、机台不确定,但能更大程度的保持生产弹性。
类似的,当工人寻求帮助时,传统的观念认为应该是谁有空谁上,而不是指定的人员。
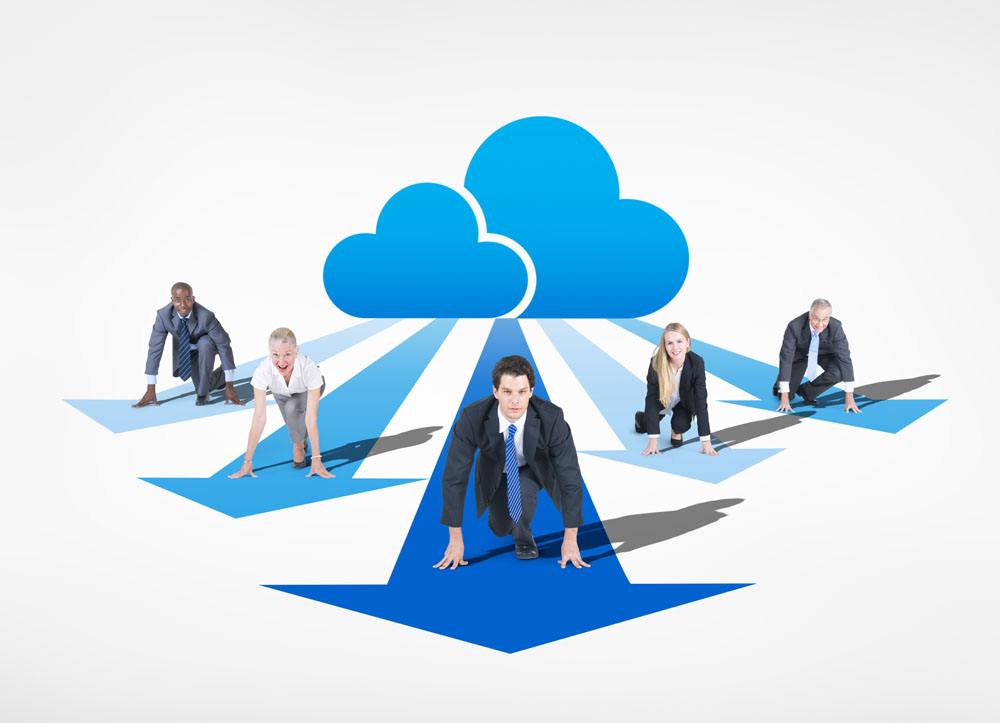
也曾见有人堂而皇之的灌输这样的“精益理念”:
“设计流水线时,应该考虑到各个工序之间能互相照应,但一个工序来不及,或出现问题时,相邻工序的操作人员可以及时进行协助。”
竟然应者云集,和者甚众。
有这样的理念不奇怪,但认为这是精益或TPS理念的人事实上下图中那样的,门都没找着。
大部分的工厂,大部分的生产,同一项工作都能由不同的机器设备或多个工作站来完成。
工厂里也习惯根据实际情况将产品交由接下来有空闲的机台和人员来进行生产,从计划到生产,莫不如此。
这样做有其合理性。
但是,这绝对不是TPS目视的生产运作模式。
再次强调。
在TPS系统中,产品或服务只流到指定的人员或机器,而不是下一个有空闲的人员或机器。
以Hermanmiller的AERON座椅的靠背安装为例。
安装工人需要塑料靠背。
安装工人发出需求(看板)。
指定的物料配送员A根据看板从线边超市备料,并将已配置好的靠背传送到装配工位。
线边超市上的靠背数量减少,最终产生物料需求。
线边超市物料配送员B发出物料需求(看板)。
仓库物料配送员C根据看板准备靠背。
仓库产生物料需求(靠背)。
物料需求(靠背)被传递到注塑供应商。
……
在这种生产线的链接下,发货需求会直接联动到注塑供应商的注塑生产。
再深一步,数量足够大的情况下,会影响到塑料粒子厂家的生产。这才是真正的“客户,生产,供应商一盘棋”。
这个原则并不是只对产品使用,当工人寻求帮助时同样适用。
在HERMANMILLER的美国工厂里,我所看到的这样求助的路径上有4个链接这么长。
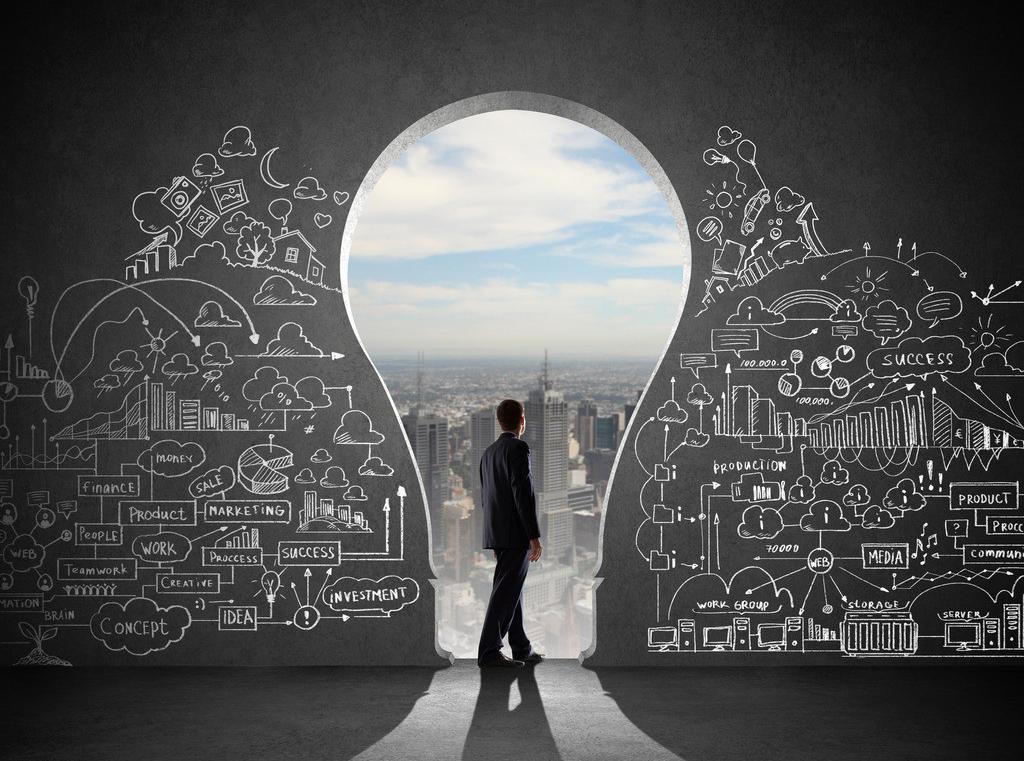
车间工人按下ANDON,发出求助需求。
FACILITATOR (救助者) A提供帮助。
STATION FACILITATOR (工位救助者) A不能解决问题,ANDON升级。
LINE FACILITATOR (生产线救助者)B提供帮助。
LINE FACILITATOR (工位救助者) B不能解决问题,ANDON升级。
SECTION FACILITATOR (工位救助者) C提供帮助。
SECTION FACILITATOR (工位救助者) C不能解决问题,ANDON升级。
PLANT MANAGER(工厂经理)提供帮助。
当然,我所见到的是98%的线上问题在LINE FACILITATOR(生产线救助者)这里就得到了解决。
在这些看似简单的方法里,重点是这些求助问题的类型,求助的模式,协助的人员都是有明确规定的并得到不打折扣的实施。
问题不除,安灯(ANDON)不灭。
为什么要这样做?
在过程设计时,有一个最基本的假设:
【生产线上每一个动作和人员都是必须的且合格的,不存在的就是不必要的】
可见,过程设计时就必须有足够的专业知识和小心。
在这个原则下,任何时候,如果工人发现他们想将生产转到别的机台上进行生产,或他们需要向指定人员之外的人寻求帮助,他们就推断出他们实际的需求或能力并不匹配他们的期望(设计)。
当这些指定的人员或机器没有空或不能胜任工作时,这就是一个问题,也就带来重新改善过程设计的机会。
这就回到那个最初的问题上来,TPS是什么?
【TPS是一个促进人们科学解决问题的系统】
03
设计好的实现路径不能更改,除非已经按流程经过明确的分析和重新设计。
为什么要按设计实施?
这其实不是一个问题。
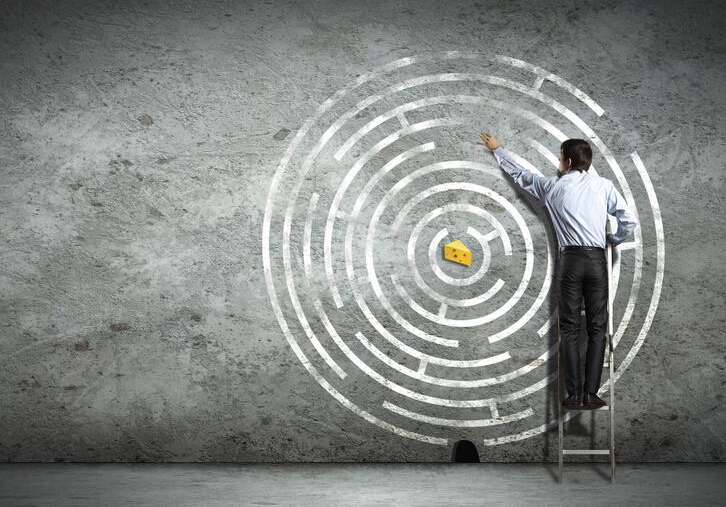
有设计不按设计实施,那你干毛要进行设计啊?吃饱撑的,没事闲的慌啊?
说起来也有道理,但做起来不那么容易,毕竟理论跟实际是有距离的。
所以av十大软件平常也习惯变通,差不多得了。
但在TPS中,要求每次都必须严格按照设计的路径来实施,不允许变通。
这样做,并不是认为初始设计是无懈可击的金科玉律。
恰恰相反,而是认为初始设计中一定有很多没有发现的问题和需要改善的空间。
只是,发现这样的问题和改善空间需要不停的“试错”。
而只有按设定条件进行无数次“试错”,你才能发现初始设计的问题与机会。
这就如av十大软件做多因子实验设计,当实验次数足够多时,av十大软件最终会发现那些av十大软件需要了解的真因和希望的优化组合。
这样,在严格按照设计要求进行运作的要求下,生产线每运作一次,生产试验就发生一次。
你生产了1000个产品,就进行了1000次试验,你生产了10000个产品,你就进行了10000次试验。
相当于反反复复对过程进行锤炼。
在这样的锤炼中,你的过程才会磨砺得越来越精巧,强劲和有生命力
文章来自网络,版权归作者所有,如有侵权请联系删除
“感谢冠卓咨询老师对项目组的全程辅导,通过做项目av十大软件学会了如何用系统科学的方法分析研究问题;开阔了av十大软件的视野并让av十大软件的十大污的软件人员明白了团队协作的重要性。”
———北京某公司总经理 苏先生