最近几年,中国大江南北越来越多的组织在导入、实施精益工具和方法。
特别是2018年10月1日通用电气公司(一百多年来都是从内部培养首席执行官)突然宣布聘请丹纳赫公司前CEO劳伦斯·卡尔普为董事长兼首席执行官。
媒体都打出的只有“精益才能拯救通用电气”的标语。不少企业家和精益从业者也提出是否可以说:精益可以救中国的免费看污的十大app企业。
与此同时,时常有企业十大污的软件者和精益圈的朋友在纠结什么是精益:是隐含吝啬、削减和裁员的含义?
是压缩——缩短提前时间,减少空间、能源、材料、紧张、过载、次品、污染、换型时间、加工时间和工作时间?[1]是5S, 看板,目视化十大污的软件,价值流程图等工具?
要正确理解什么是精益,笔者强烈建议大家重读精益的经典之作《精益思想》。
在这本著作中,精益大师詹姆斯·沃麦克和丹尼尔·琼斯全面阐述了精益思想的五项基本原则。
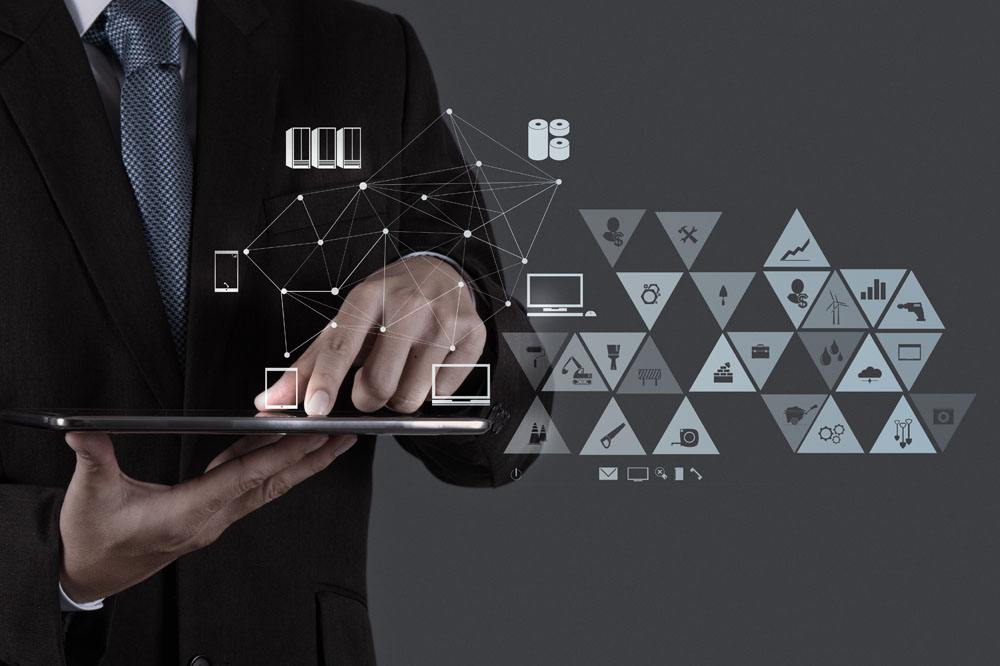
原则1:价值
价值,指的是体现在商品里的社会必要劳动,它通过顾客愿意付的价格来体现。在完全竞争的买方市场中,价格是由顾客决定的。
顾客不会为不必要的劳动付钱。因此,企业应千方百计地减少在提供产品或服务时不必要的浪费。
举个简单的例子,比如加工一个桌子,因为测量失误造成桌面比标准的高度高了5厘米。
然后操作者通过返工,将桌子的高度降到标准高度。顾客是否愿意为该桌子的返工付钱?当然不愿意。
再如,我的包裹时从郑州运往上海的,快递公司投递错误将它运到北京,发现错误后又从北京运到上海。
顾客是否愿意为超长距离的快递服务多付呢?不仅不会多付,快递公司没准还要因延时赔付违约金。
原则2:价值流
价值流,即创造价值的过程。在典型的免费看污的十大app型企业的生产过程中,有三个关键流程:产品设计过程、信息传递过程和物料流动过程。
产品设计大致包括概念提出、设计产品、编制工艺、产品试制等。信息传递过程包括订货、排产和发货等信息的传递。
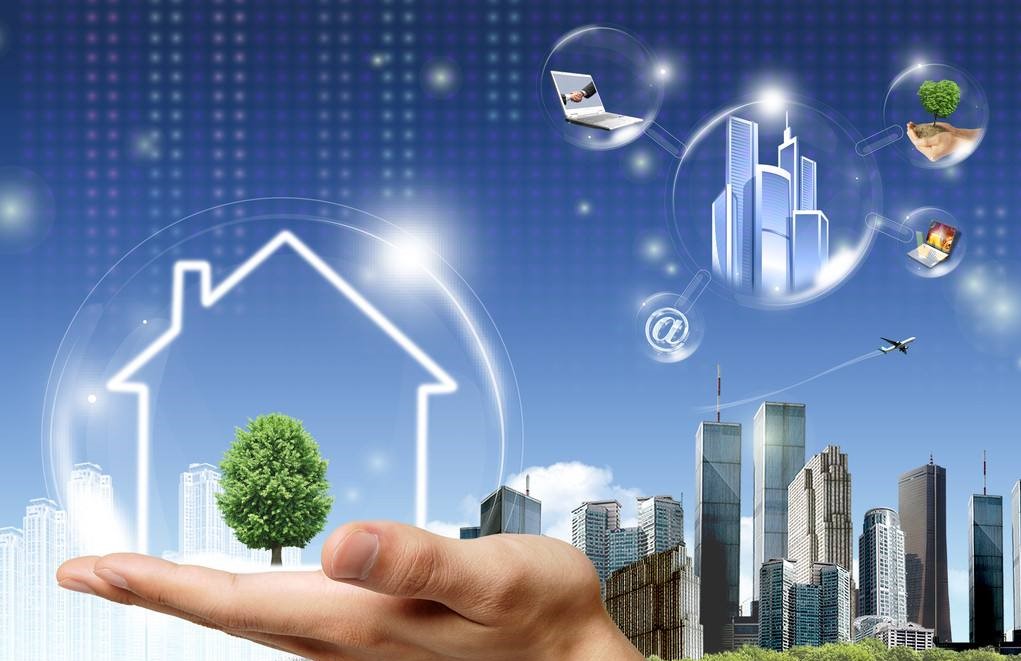
物料流动过程包括原材料采购、产品加工和产品交付等过程。
在导入实施精益的过程中,av十大软件可以借助价值流图(ValueStream Map)来分析企业的价值流,从而发现不创造价值的浪费,最后采取措施消灭浪费。
价值流范围的大小取决于企业改善活动的大小。若只是做一些小的改善(kaizen),企业可以在某一个或几个部门内对价值流进行分析。
若想进行突破性改善,企业可以对整个公司甚至是整个供应链进行价值流分析。一般情况下,改善所涉范围越大,取得的效果越大。
2018年6月7日,余锋摄于丰田公司在美国得克萨斯州的免费看污的十大app基地。
《精益思想》一书将价值流中的活动分为三类:
能创造价值的活动、不能创造价值但在目前的技术条件下又不得不做的活动(Ⅰ型浪费)和不创造价值且可以立刻去除的活动(Ⅱ型浪费)。
原则3:流动
流动,即要求生产线流动起来,最终达到单件流作业。流水作业可以暴露出生产中存在的问题。
因为,一旦流水线上任何一个环节出现问题(缺料、设备故障、零部件质量问题,等等),就会导致流水作业的停止。这样,就可以及时发现并改正问题,从而提高生产效率。
流水作业还可以大幅度缩短产品的生产周期。因为从原材料到半成品、从半成品到成品,整个过程处于流动状态,不会出现物料的停滞现象。
传统的生产是将生产过程按工艺分成不同的部门。
零件以批量的形式在一个部门加工完之后再转到其他部门加工下一道工序,这样会延长零件的周转时间。
另外,即使在同一个部门,操作者习惯大批量加工同一种零件。
这样零件在各个工序之间存在大量的等待浪费。因此,推行精益思想,必须与部门化和批量化加工做斗争。
原则4:拉动
拉动,即顾客的需求拉动企业的生产。
拉动起源于超市的补货系统,服务人员完全根据消费者买走商品的数量和品种进行上架,采购部门根据消费者买走商品的数量和品种进行采购。
这样,超市就避免了过量的采购和库存,进而降低了经营的风险和成本。
该原理同样适合其他类型的企业。以丰田汽车为例,顾客订购什么样的车型,它就生产相应的车型,没有订单就不生产,从而避免汽车的过量生产。
企业内部的零件生产也是如此,上游工序按下游工序领取零件的品种和数量进行生产,没有领取就不生产,从而避免零件的过量生产。
其实,过量生产是精益生产的万恶之首。因为,一旦技术更改,或者市场从此不再需要此种产品,将会造成极大的浪费。
另外,如果采取拉动式生产,销售预测的风险将会大大的降低,因为更多的生产信息来源于顾客的订单而不是估计。
原则5:尽善尽美
尽善尽美,即精益求精。组织在经历了前面的四个环节之后,会在各个方面取得突破性的进展,各个环节会逐步进入良性循环状态。
但是,改善永无止境。企业依然存在很多不合理的地方,期待av十大软件进一步深入地去发现和解决。
2017年,尽管霍尼韦尔公司特性材料与技术集团在亚太区的销售收入和利润双双创造了历史新高,员工们还是提出并实施了一万多个改善项目。
企业存在两种类型的浪费。在进入良性循环后,av十大软件可以尝试去除Ⅰ型浪费。尽善尽美是一种对完美境界的不懈追求,久而久之,企业就会获得一种质的提升。
笔者希望企业家和精益实践者在导入、实施精益的过程中不时回到精益的原点,重温精益的五项基本原则,把你的组织和团队转型成所在行业的丰田、丹纳赫或霍尼韦尔。
文章来自网络,版权归作者所有,如有侵权请联系删除
“感谢冠卓咨询老师对项目组的全程辅导,通过做项目av十大软件学会了如何用系统科学的方法分析研究问题;开阔了av十大软件的视野并让av十大软件的十大污的软件人员明白了团队协作的重要性。”
———北京某公司总经理 苏先生