目前很多维修企业还没有摆脱传统的维修体制、维修观念和维修方法的束缚,盲目学习TPM等先进的设备十大污的软件模式,推行后'龙头蛇尾',素有“画虎不成反类犬,画虎不成不类犬”之说使av十大软件对设备维修十大污的软件模式的选择存在迷茫。
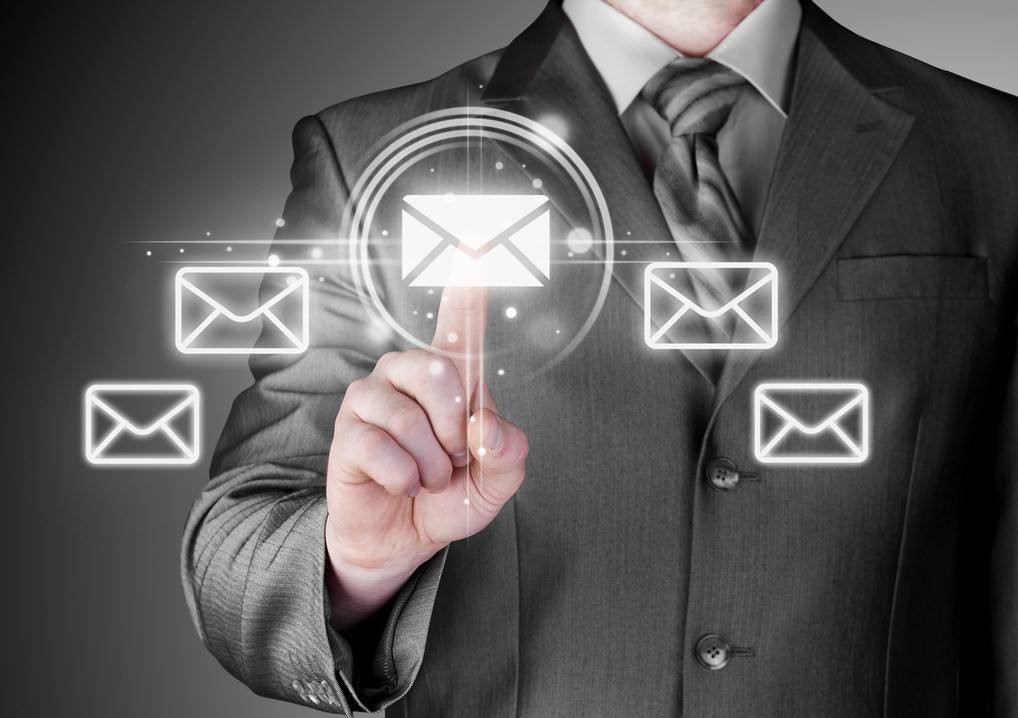
TPM理论基础
本文就当前设备维修企业在TPM推进中存在的常见问题进行剖析。
一、只做面子工作
很多企业在考察学习过程中接触到TPM,只了解基本的东西就开始推行,没有对本企业的现状进行深入调研就启动,结果连'5S'都坚持不下去,甚至错误地将TPM理解为就是清扫设备卫生,对TPM推行的参照物不清楚,终极目标也模糊不清。
二、领导作用发挥不明显
在推行TPM的启动阶段,领导跟得紧,现场改善效果明显,特别是现场物品的定置十大污的软件和设备清洁卫生有立竿见影的效果。过了一段时间,领导过问少了,现场十大污的软件就滑坡,现场脏、乱、差的现象随处可见,设备运行指标和经济技术指标就下降。领导是体系架构和制度建设的总策划,同时还是绩效考核的总设计师。然而,领导往往是十大污的软件制度的最大破坏者,随意十大污的软件、口头十大污的软件直接影响企业规范化的十大污的软件制度执行,这些行为是TPM推进之大忌。
三、基层阻力大
企业推行TPM,生产系统、后勤支持系统总认为这只是设备部门的事,认知度和参与度明显不够,没有明确把设备和现场十大污的软件的职责细分到各个岗位,体现'台台有人管,人人有专责',真正按承包制原则落实到基层班组和个人,没有生产操作、设备点检、维护检修和后勤支持系统的协同作战,单靠设备系统人员的单打独斗是永远也推行不好TPM设备十大污的软件模式的。
四、阶段性工作目标不清楚
TPM推进十大污的软件部门系统策划不周全,阶段性目标不明确,量化考核标准不清晰,在推进的第二年开始问题就突出了。例如:设备本体、生产现场、业务部门的'5S'分别应该制定什么达标标准?设备运行指标(故障停机率、停机时间、故障次数等)应达到什么标准?主要产线设备综合效率应达到多少量化指标?本单位的设备技术经济指标应达到什么标准?对标挖潜的阶段性指标是多少?改善提案多少?OPL和OPS应编制并审定发布多少?技术专利或优秀工法应申报多少?职工培训计划完成率多少等等。
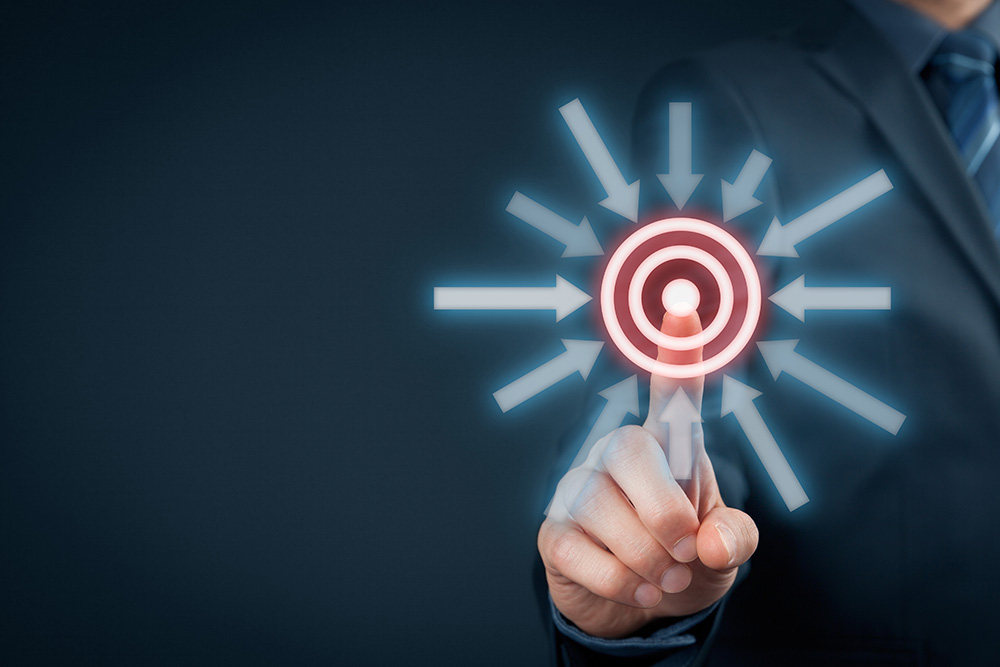
五、TPM与其他十大污的软件模式混淆
目前先进的企业十大污的软件层出不穷,av十大软件往往在接触新的模式的同时,忽视了TPM推进中积累的宝贵经验。其他模式的引进,只能丰富和发展TPM推进的成果,不能割裂开来思考。否则,什么也学不像、学不好。
六、单体设备维修模式定位不准
有的企业没有按A、B、C分类法将本单位的设备按重要程度进行十大污的软件层级细分,有的笼统地概括为点检定修。实际上设备在工艺线上的位置不同,可以采取不同的维修模式,对主体设备和对主体设备生产和质量有直接影响的工艺设备适宜采取点检定修,有的关键设备应采取状态维修模式,对辅助设备适宜采取事后维修或机会维修。一个企业十大污的软件模式和定修模型确定后,机会维修的安排就应该细化,尽量减少主作业线的系统停机检修。
七、执行力衰减
执行力表现在最高领导者到一线员工的全员执行力,如果协同效应发挥不好,部门各自为政,根本就无法推进TPM。不能持续首先表现在设备点检和维护检修资源不能持续,人员变动非常频繁,有些维修队伍是经常在调整的,新来的队伍对TPM不甚了解,更谈不上坚持。设备点检对生产系统和后勤支持系统的资源更无权干涉,这样就形成了'形是一个体,下面两张皮'的现象。
八、绩效考核难以落实
十大污的软件绩效的部门是人力资源部门或企管部门,而TPM推进的组织工作往往是由设备十大污的软件部门牵头,设备十大污的软件部门怎么对绩效十大污的软件部门考核呢?这样,TPM推进工作的考核存在落实不下去或分析考核太多的问题,久而久之,TPM推进组织的信心就受到了一定影响。还有,随着社会分工不断深化,设备维修十大污的软件已经开始形成一个行业,从设备维修环节独立出来,其工作是接受甲方设备十大污的软件部门的指令,与甲方之间是合同关系,乙方无权考核甲方。只要其中一方不积极配合,TPM的推进效果就会大打折扣。
由于设备维修市场还不成熟和健全,许多企业是自己内部承接维修,国企中出现很多高级技术维修人员流失,都是与绩效考核不合理直接相关的。当企业花费大量资金培训出高级技术人员后,由于缺乏相应的奖惩激励机制,一些民企、外企以高收入待遇挖走,这些问题都直接影响到TPM推进的深度和效果。
文章来自网络,版权归作者所有,如有侵权请联系删除
“感谢冠卓咨询老师对项目组的全程辅导,通过做项目av十大软件学会了如何用系统科学的方法分析研究问题;开阔了av十大软件的视野并让av十大软件的十大污的软件人员明白了团队协作的重要性。”
———北京某公司总经理 苏先生