数字化工厂由设备、机器人、AGV、网络、信息数据等构成,集成了产品免费看污的十大app过程和工厂模型的数据库,以提高产品的质量和生产过程所涉及的质量和动态性能。通过借助计算机,对整个生产过程进行数据采集,并可进一步扩展到整个产品免费看污的十大app过程的全生命周期,将打通产品设计和产品免费看污的十大app之间的桥梁,实现信息的集成。而生产车间是组成工厂最重要的组成部分,实现了生产车间的数字化,基本上完成了数字化工厂最核心的部分。在数字化系统建设中以数据的可视化十大污的软件和应用为核心,而非简单注重完全的自动化程度。利用PLM系统实现主数据流和工业网络、智能装备、智能仓库、智能系统等方面系统集成,实现数据流贯通与共享。
1 数字化车间硬件平台搭建
1.1 智能化生产
智能化在引入数控机床、机器人等生产设备并实现生产自动化的基础上,再以ERP、MES 等十大污的软件软件作为中枢十大污的软件系统,以视觉相机、RFID标签、扫码器、条码、传感器等为组件,以NC数控系统或PLC为控制单元,以现场总线 PROFIBUS、工业以太网PROFINET、MODUBUS等通信技术为传输网络。能够借助完善的系统获取状态信息、传递控制指令,以此实现科学决策、智能设计、合理排产,监控设备状态,提升设备使用率,指导生产运行,让自动化生产智能设备高效运转。
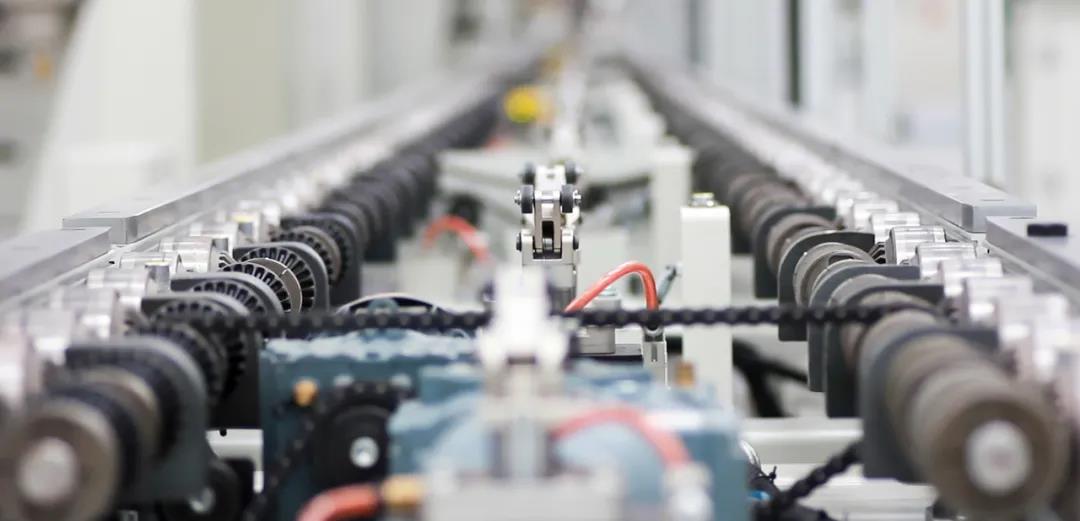
1.1.1 智能硬件
智能化生产免费看污的十大app单元是将一组能力相近的加工设备和辅助设备进行模块化、集成化、一体化的聚合,使其具备多品种少批量产品的生产输出能力。打造智能免费看污的十大app单元是开启智能化道路行之有效的切入点。为各车间配置智能免费看污的十大app单元,“智造单元”是一种模块化的小型数字化工厂实践,整个单元由自动化模块、信息化模块和智能化模块三部分组成,以“最小的数字化工厂”实现在多品种小批量的生产智能化。在加工领域,注重从单一功能型设备向多功能型设备过渡;在装配领域,突破人工操作的枷锁,逐步由人工操作向人机协作、自动化作业转变;不断发掘高精尖设备,致力于质量检测、SPC工站建设;将传统、简易的人工搬运等,采用机器人配合视觉定位技术全部实现自动化搬运。
1.1.2 智能设备互联
智能化生产车间以信息化作为根基,通过将生成车间的不同设备与通讯网络连接,收集设备的状态数据和质量数据,并作为数据采集和分析的基础。对不同生成设备,采取不同的数据采集方式:对存在数据接口的设备,如加工中心、磨床、PLC控制器、机器人、仪器仪表等,通过Profibus或Profinet网络将设备数据传输到网关;对于没有数据接口的设备,通过外接传感器完成设备状态采集,提升通讯能力,可采取有线或无线两种方式进行,数据传输到网络后,通过边缘计算方式完成数据就地分析和存储,对于数据分析结果汇总,并采用有线或无线的方式,存储到云服务器进行数据显示和后续数据分析工作。设备的联网接入需完成三项重要的工作:硬件接口的连接、软件数据接口互通、接口规范定义。
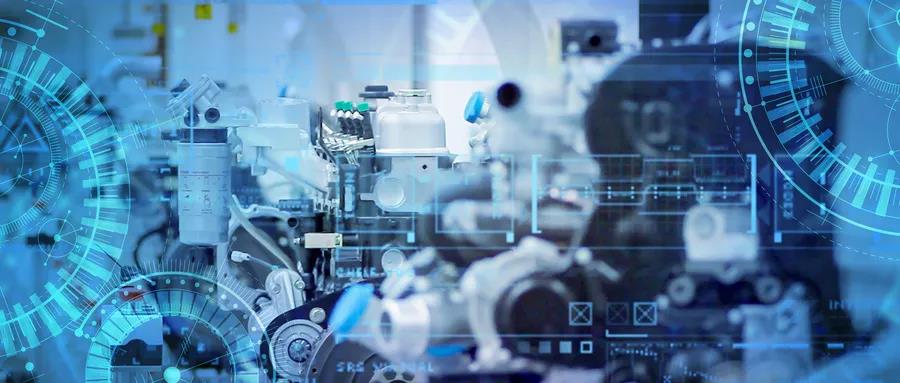
1.1.3 智能设备数据采集
完整的免费看污的十大app设备应具备完善的档案信息,包括产品编号、产品描述、产品状态、产品时间戳等信息。按照已定义的通信接口,与其他设备、装置以及执行层实现设备和数据的互联互通。对收集完成的数据进行分析,筛选出合格数据,对于不合格数据采用自动处理和人工处理两种模式完成,最终保证产量质量状态的稳定,并可满足产品的质量追溯。
1.1.4 智能免费看污的十大app执行系统
建立MES免费看污的十大app执行系统,运用生产调度十大污的软件、工艺执行与十大污的软件、过程控制十大污的软件、排程十大污的软件、质量十大污的软件、设备十大污的软件等模块,可时刻十大污的软件和展示生产免费看污的十大app全流程。通过开发数字化生产免费看污的十大app执行平台,打通计划、生产、物流、设备间的数据流,构成计划、控制、反馈、调整的完整系统,通过规范的定义接口实现计划、命令的传递和实际生产的无缝衔接,使生产计划、控制命令、信息数据在整个 MES 系统、过程控制系统、自动化体系中透明、及时、顺畅地交互传递,最终实现生产全过程数字化,打造数字化生产车间。
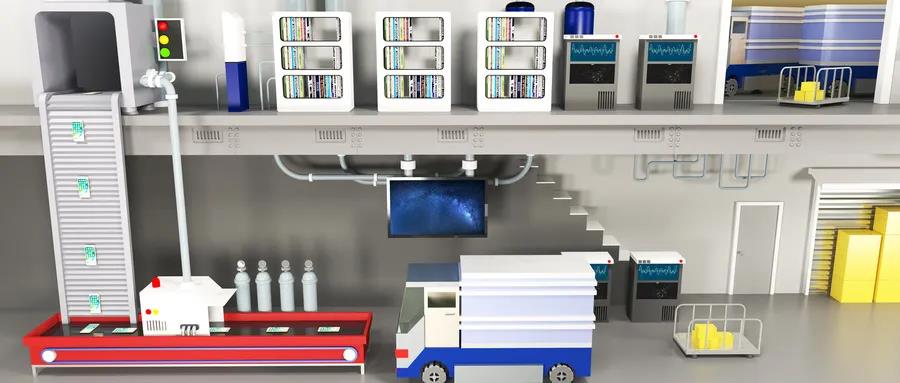
1.2 智能化物流仓储
物流仓储是免费看污的十大app业中极为重要的一环,通过应用智能物流仓储系统可快速完成产品原材料、产品配套件、成品件之间快速流转和输送工作,通过采用堆垛机输送方式和立体仓库存储方式提升仓库货位周转效率,降低仓库转运过程造成的人工成本,提升转运效率,实现仓库储流数字化管控和智能化运输。
建设智能物流仓储系统,完善系统组成架构:设备层、操作层、企业层。设备层建设立体仓库、智能叉车、码垛机器人、提升机等仓储设备,建设AGV、智能托盘、物流机器人等物流设备、RFID、机器视觉、智能摄像头等识别设备;操作层增加 WMS、WCS、TMS 等运维软件;企业层则对接ERP、CRM、SCM等十大污的软件软件的采购、计划、库存、发货等模块,融入总系统的闭环中。
2 数字化车间平台搭建
工艺是将研发设计的产品赋予灵魂的重要一环,推进数字化技术应用并覆盖于产品的设计、工艺、免费看污的十大app全生命周期,是实现智能免费看污的十大app的关键一点。通过工艺数字化信息平台建设,将打通设计、工艺、免费看污的十大app之间数据流,实现上下游高效协同,通过数字化工艺的深化应用,工艺一致性将实现100%,20%的问题将在规划早期被验证发现,产品的生产准备周期将缩短20-30%。
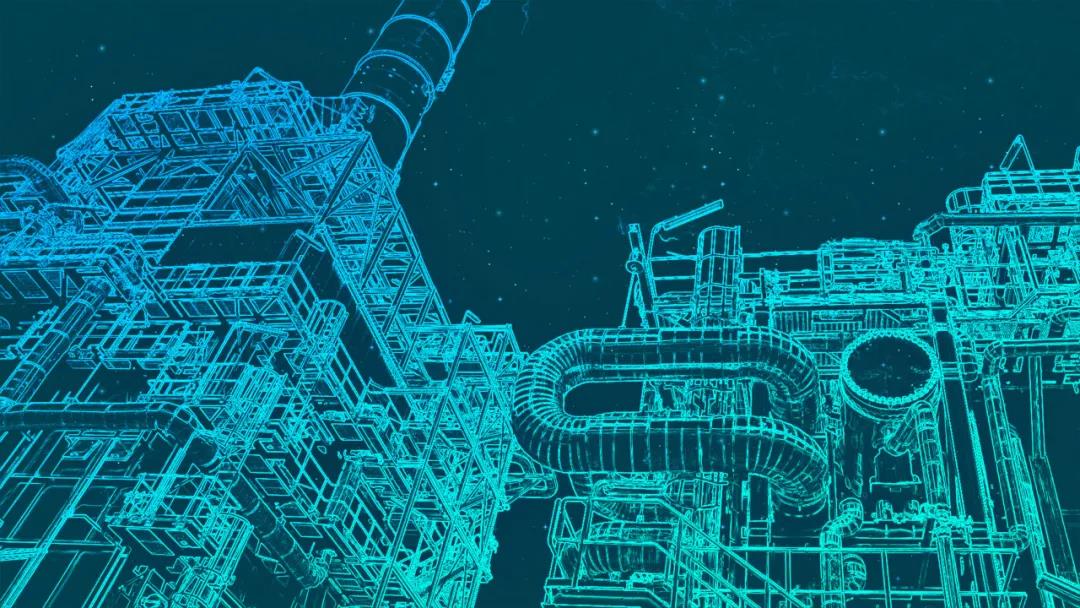
2.1 数字化工艺平台建设初期
完成基础功能模块开发及应用。产品准备十大污的软件按照APQP实现管控,系统化管控项目进度及交付物;BOM及工艺十大污的软件,实现数据及时、准确,提高工艺一致性及标准化;变更十大污的软件实现正向与逆向的闭环十大污的软件,提升变更执行质量;实现工艺资源管控,实现知识积累、共享和重用。
2.2 工艺数字化平台建设中期
实现工艺创新性十大污的软件:通过工艺仿真技术,实现三维数字化工艺规划及验证,对工艺合理性进行虚拟仿真及评估;实现三维工艺下厂,提高工艺可视性;通过产线仿真技术,对生产线的装备、物流、工艺、节拍、人员、生产过程等进行仿真、优化及十大污的软件。
2.3 工艺数字化平台建设后期
实现工艺数字化技术深度应用:通过数字映射技术,实现实际生产与虚拟生产联动,可以及时修正生产中的偏差及问题,实现更科学更智能的生产。加强数字化技术团队建设,成立专门的项目团队负责技术研究及系统建设,推进工艺数字化提升工作开展。
建立数字化标准体系及业务流程,根据数据流、业务流传递特点及上下游关系制定完善的数字化流程,实现十大污的软件创新促进技术创新、技术创新推进十大污的软件创新。加强数字化基础建设及设计免费看污的十大app辅助工具开发。从软件基础环境、数据库支撑平台、网络信息环境、信息安全体系等基础方面进行投入和建设。
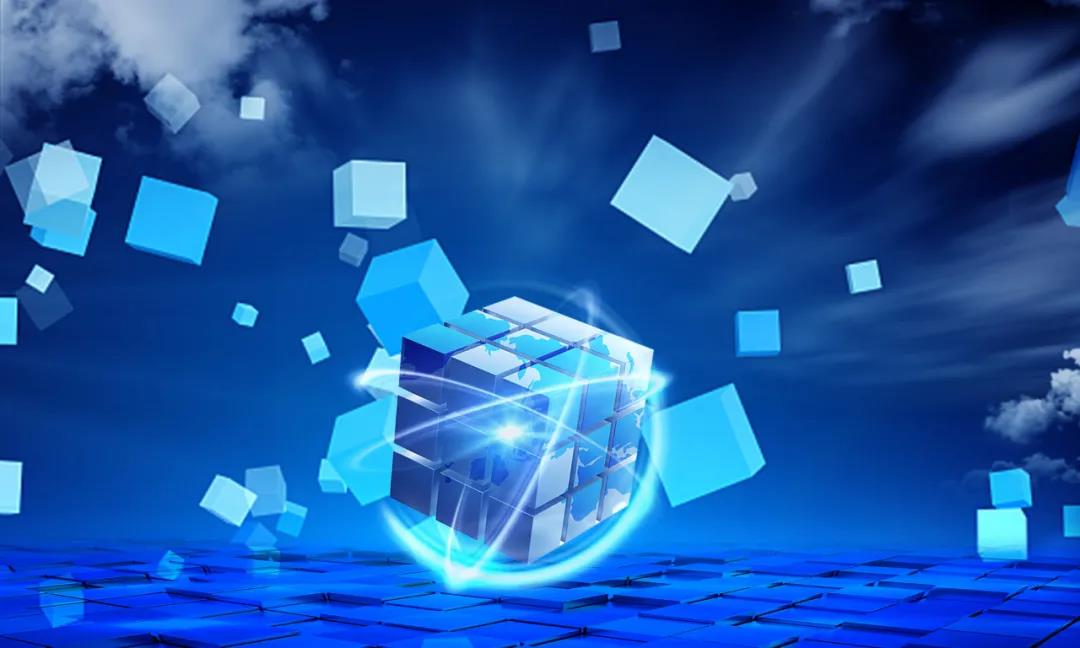
2.4 仿真系统应用
结合产线数模、物流仿真等,实现产线仿真,对生产线的装备、物流、工艺、节拍、人员、生产过程等进行仿真、验证、优化及十大污的软件。通过数字映射技术,实现实际生产与虚拟生产联动,当生产线出现问题时能够实时反馈至虚拟系统,通过虚拟系统验证后更改虚拟参数,可实现生产线同步更改,这样就可以及时修正生产中的偏差及问题,实现更科学更智能的生产。
通过与MES、ERP、工艺装备、工艺资源等车间系统深度集成,实现数字化车间技术研究与应用,为实现智能化车间、产线大数据分析等奠定基础。
3?结论
在数字化车间建设与实施过程中,关键点是引用PLM系统实现主数据流贯通和系统集成,数据流贯通保证了数据的准确、及时、共享,系统集成实现了数据的互联互通。并在此基础上进一步实现数据可视化、透明化。顶层规划很重要,在项目开始阶段,完成顶层设计方案,确保项目实施过程可控性和可预知性。智能工厂建造过程通过数字化双胞胎,实现全集成可视化工厂。实现软件和硬件的智能互联,通过设置标准网络接口实现机床间互联互通。
文章来自网络,版权归作者所有,如有侵权请联系删除!