精益生产(Lean Production)是一种以顾客需求为拉动,以消灭浪费和快速响应为核心,特别适合于多品种小批量的生产免费看污的十大app模式;其核心就是“精简”、“瘦身”,通过减少和消除产品从设计开发到售后服务中一切不产生价值的活动,缩短产品交付周期,提升企业资金流转率和利润率。
许多企业在导入精益生产理念和方法后,很少认真地对整个产品的价值流进行分析,马上就进入大规模的消除浪费活动中,虽然可能改善了产品价值流的一小部分,使之流动比以前顺畅了,但是其它部分的问题仍会导致大量库存,最终的结果是没有降低成本,甚至有所增加。如果仅仅局部实现了精益,那么改进效果的持续性就会受到限制,不能实现如大野耐一所说的“在全过程中减少浪费”,这将会导致精益生产的实施无法持续进行下去。
不同行业、不同企业的情况是千差万别的,av十大软件在实施精益的过程中,经常会被企业杂乱无章的背景所迷惑,无从下手。在这种情况下,就需要有一个有效的工具或方法,能够让av十大软件找出浪费及其原因之所在,然后将其消除,这个工具就是价值流图析技术。
价值流图析技术作为一个有效的工具,可以通过作图的方法,帮助企业梳理整个产品价值的流动,而不是只考虑孤立的某个生产工序,从而使企业能够对整个价值流进行持续的、系统化的改进,提高企业的效益和市场竞争力。
av十大软件在进行价值流图析之前,首先要搞清楚什么是价值流,什么是价值流图。
价值流是指从原材料转变为成品并交付给客户过程中的全部活动(其包括原材料的搬运、加工、组装、检测、储存、出货等)。它包含了增值活动和非增值活动,那什么样的活动是增值的呢?其实活动的增值与否是以客户愿不愿意付钱为标准的,客户认为有价值的,愿意给钱的活动就是增值活动。

价值流图是以图形及文字描述整个生产流程,它是一个基本的分析工具,记录每一个工序及每个“价值流”的相关信息。
av十大软件该如何应用价值流图进行生产流程分析呢? 一般会基于问题解决的思路分7步骤进行分析:
步骤一:选定需要分析的产品族
遵循二八原则(20%的产品影响80%的营收),可以确定对公司影响较大的产品类别。
步骤二:现状调查
从订单十大污的软件到出货全流程的信息流及价值流梳理,在产品加工环节可从设备综合效率OEE、产品加工周期C/T、一次合格率进行数据采集。
步骤三:绘制现状图
绘制价值流图析现状图的意义就在于通过图析发现工厂生产过程中存在的浪费,从下图av十大软件可以看出,318.41秒的生产时间只占整个周期时间5.65天的0.078%,大量的时间浪费在库存和等待上了。通过分析原因,找出关键的浪费及其改进方案并予以实施-即通过实施精益生产来消除产品价值流中的浪费。
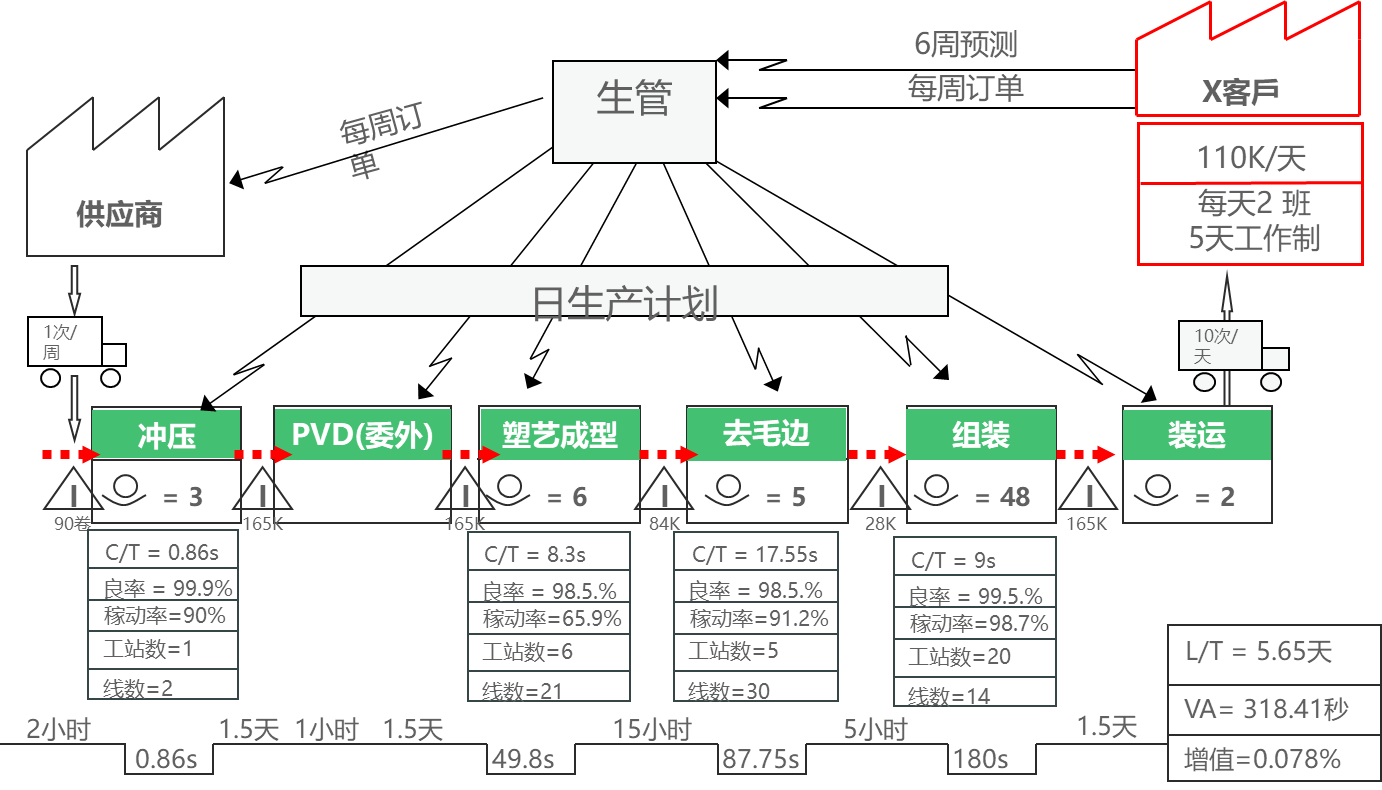
分析现状的目的在于解决价值流中的问题,而这些问题要在未来状态图的制定中通过实施精益价值来予以解决。
这里简单介绍现状价值流图的绘制方法:
1)绘出客户及客户需求信息(如图右上角客户要求框所示,主要应了解客户的需求量、种类、交付周期和要求等);
2)绘出产品装运过程(Output);
3)绘出产品加工工艺流程;
4)收集并记录每个生产过程的数据(在每个过程数据框下记录的主要数据包括生产节拍、换型时间、操作人数、有效工作时间、设备时间稼动率、废品率等与过程改进数据,注意:这些数据必须现场收集的,而不是某些资料记载的);
5)标明工序间的库存(应对所有库存,包含线上在制品库存进行盘点,然后记载库存于图中三角下面);
6)添加原材料供求信息(如图左上角,了解主要供应商的供货情况)
7)增加原材料及成品的移动线;
8)完善物流(添加WIP移动线,工序间的虚线箭头部分);
9)信息传递,画出信息流(了解、记录客户订货、生产计划、原材料订货过程的信息传递途径及信息,画出信息流,如上图上部所示,标示出客户订单、材料订单和生产信息传递途径和方法);
10)画出生产时间线和计算相关数据(将库存数量按照客户需求节拍转化为时间,与生产过程时间数据一同画在时间线上,求出生产过程时间占整个时间的百分比)。
步骤四:检讨问题点
针对步骤三绘制出来的现状图进行分析,分析的准则如下所述:
1.按照客户的节拍生产(使得生产过程的节拍与交付客户节拍保持一致,实现准时化生产);
2.尽可能开发连续流程(尽量消除和减少库存和等待,这样生产过程就可以连续进行);
3.在无法实现连续流动的地方采用看板或超市拉动十大污的软件(对于节拍相差悬殊,种类繁多的过程,如图中冲压到塑艺成型这样的无法流动过程,可以采用看板十大污的软件或超市十大污的软件);
4.努力将顾客订单计划只发到一个生产过程(保证信息的一致性);
5.在定拍过程按时间均匀分配多品种多产品的生产(多品种、小批量的混流均衡生产,要求后工序通过减少换型时间和生产批量来提高对本工序过程变化的响应速度,这样可以尽可能地减少在制品库存量)。
步骤五:绘制未来图
未来状态图是av十大软件进行精益转化的目标蓝图。依照精益思维和精益价值流的准则来分析前面做出的现状图,使av十大软件可以发现存在很多方面的浪费,以便av十大软件去消除。
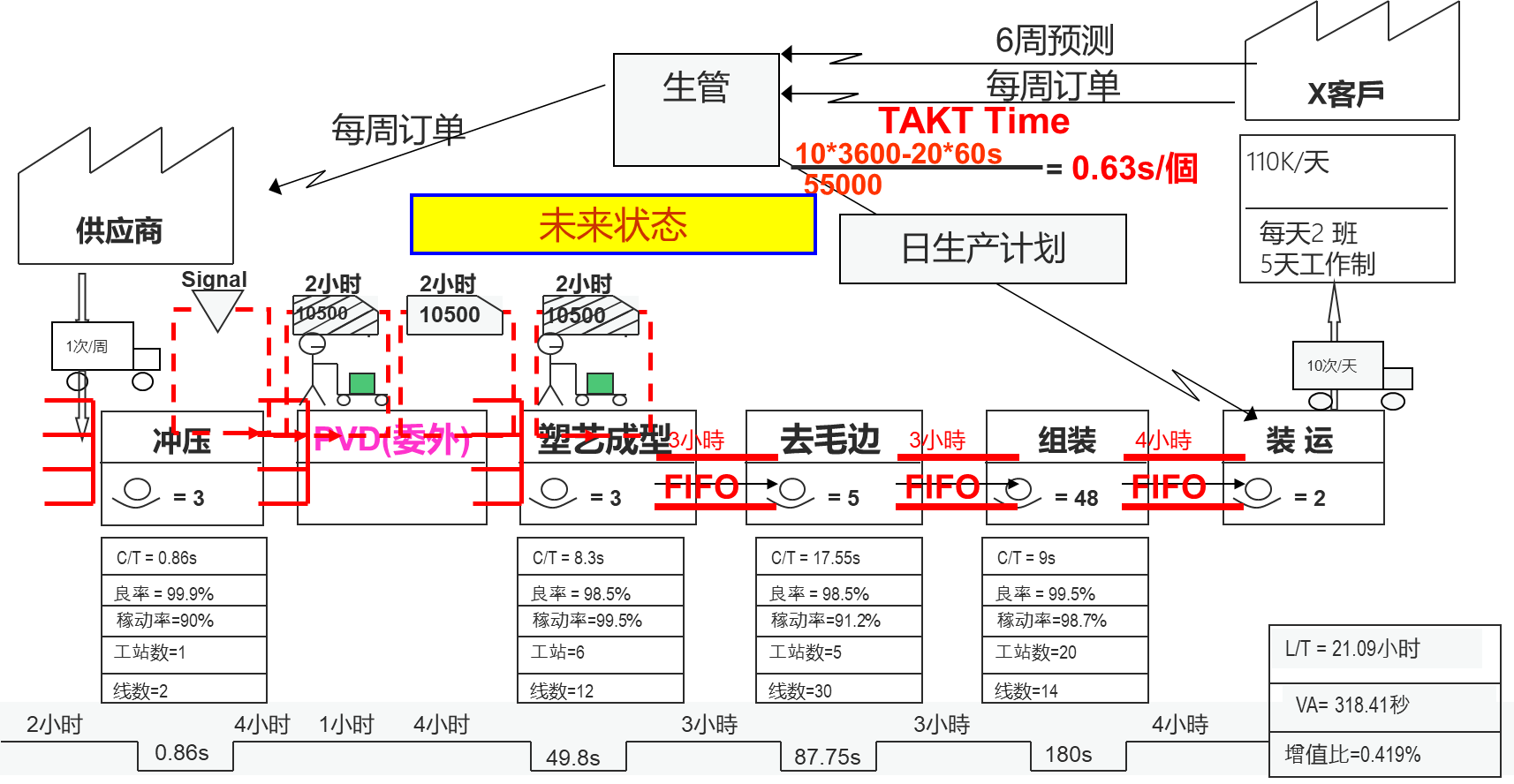
步骤六:制定改善计划
1.分解价值流步骤
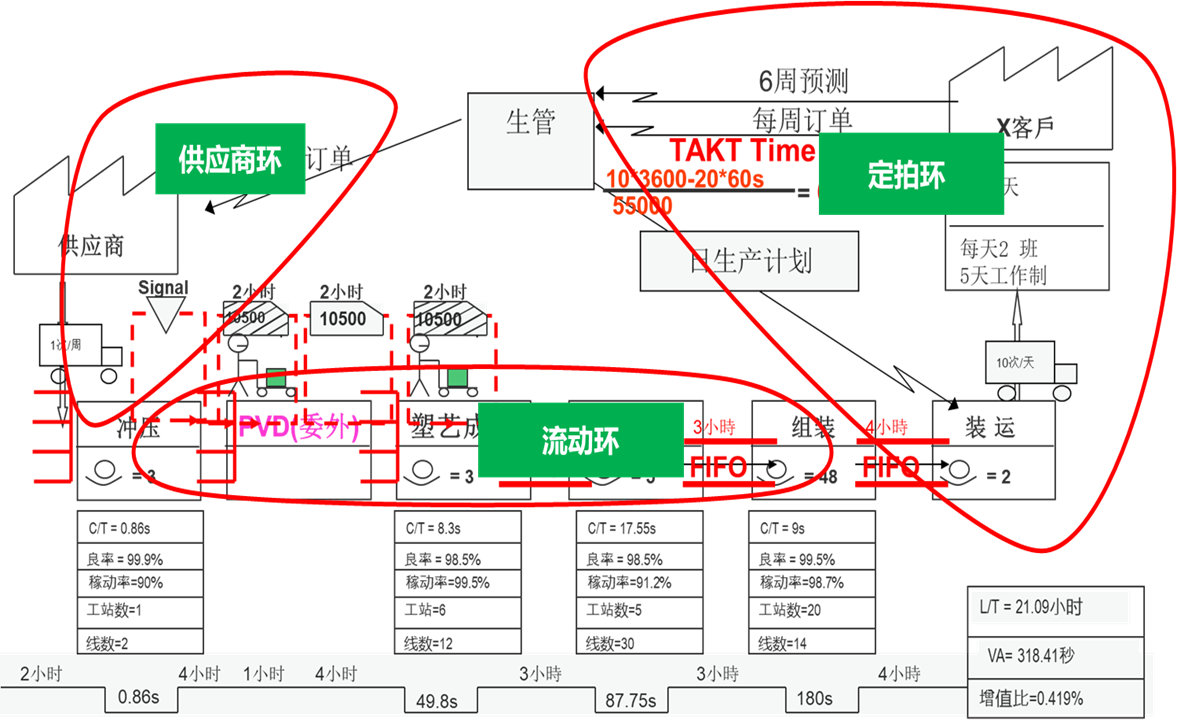
1)开发一个以顾客节拍为基础操作的连续流;
2)建立一个拉动系统控制生产;
3)引入均衡生产;
4)落实改进,从而不断地消除浪费、减少批量、缩小超市存货、扩大连续流程的范围。
2.制定价值流改善计划
步骤七:实施改善计划
1.绘制改善中的VSM图;
2.跟进实施改进的状况;
3.改善评审及总结;
进行下一阶段改善(成果固化后)。
本文为冠卓咨询原创文字作品,任何人或组织不得对本文进行篡改,转载或以盈利为目的行为,一经发现,将负法律责任。