
SPC即过程统计控制,是利用统计方法对过程中的输入进行管制,从而达到改进与保证质量的目的。SPC强调以全过程的预防为主,主要工具为控制图,控制图能发出信号提示一个在稳定状态的过程正受到外来因素的影响。
建立SPC控制,确保生产过程在管控的状态下并识别及降低产品品质的变异代替事后的检验把关显得尤为重要。
以下围绕北京冠卓咨询公司为H企业建立的SPC实例进行展开,阐述如何建立过程SPC控制。
首先,冠卓咨询为H企业就SPC的建立制定了一个完善的推进计划流程,以此作为H公司建立SPC的工作思路指引:整体思路流程围绕PDCA四个阶段,细分至14个步骤进行展开。
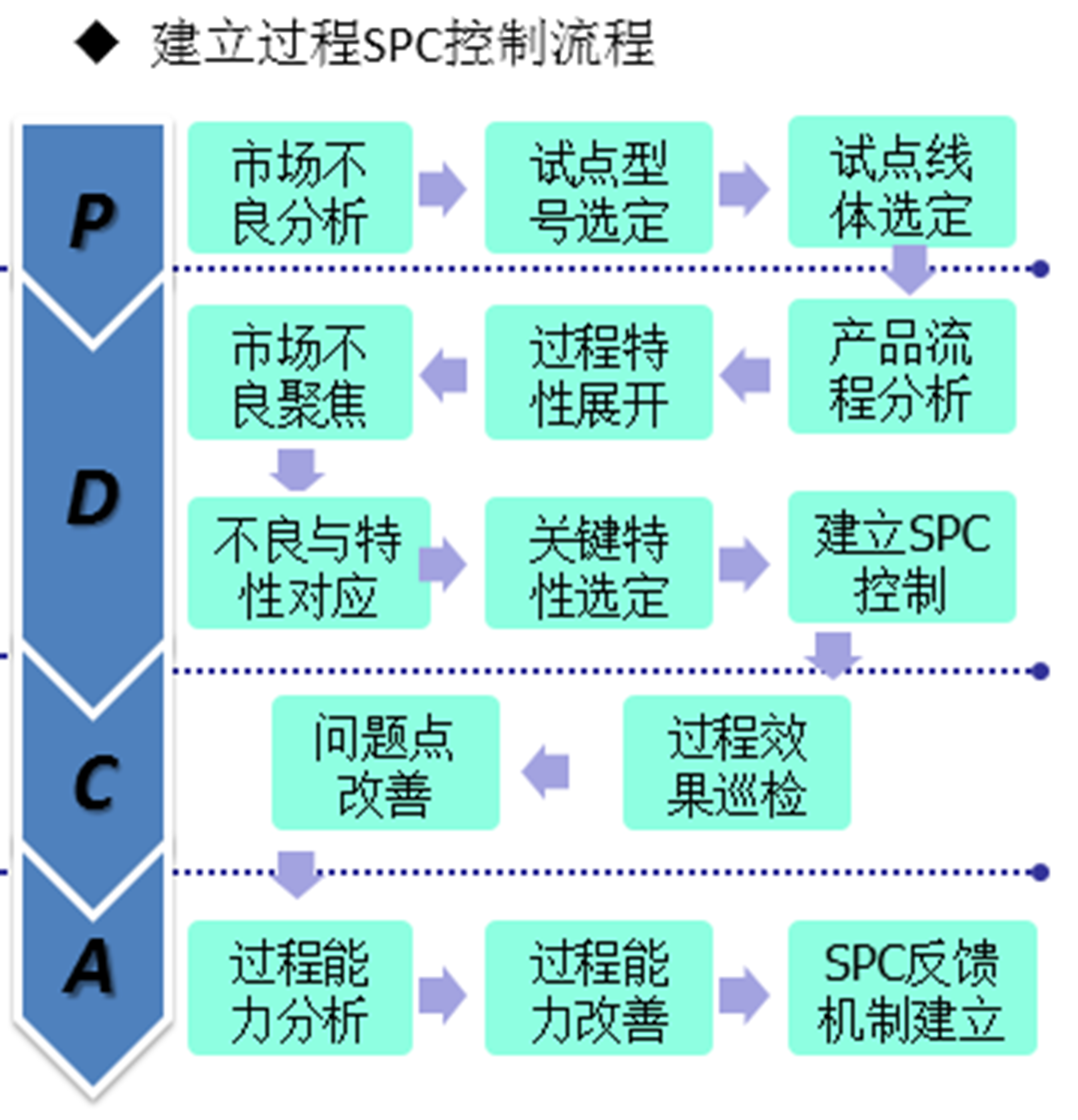
STEP1-计划(Plan):
此阶段主要是决定SPC控制的试点线体及型号。av十大软件都知道很多公司有很多的生产线或生产单元,不同的生产线同时生产不同的产品型号,不同型号的过程输入又不尽相同。如何在不同生产线的不同型号建立SPC控制呢?一网打尽的方法显然行不通,可行的办法就是选定某一产线的某一产品作为试点并以此复制展开。
此阶段主要分为以下3个步骤进行:市场不良分析->试点型号选定->试点线体选定。此阶段的三个步骤以客户的关注点作为切入(如市场不良率),并以此选定所对应的产品型号及线体。
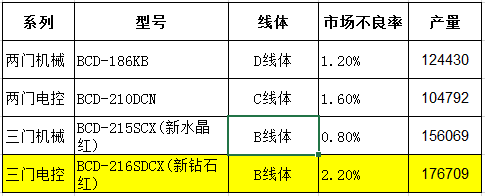
STEP2-实施(Do):
此阶段共分为6个步骤展开:产品流程分析->过程特性展开->市场不良聚焦->不良与特性对应->关键特性选定->SPC建立。
实施阶段为SPC控制建立的重点阶段,此阶段所涉及的工作量也是整个过程占比最重的阶段。此阶段的内容主要是对所选定的产品型号进行加工过程步骤的细化并对每个细化的步骤进行相应输入特性的展开,同时围绕市场的不良现象聚焦到相应的工序步骤,结合不良及输入特性进行匹配并确定最终需进行控制的关键输入特性,最后围绕选定的关键特性决定SPC的控制方案。
产品流程分析及特性展开(部分)

市场不良聚焦
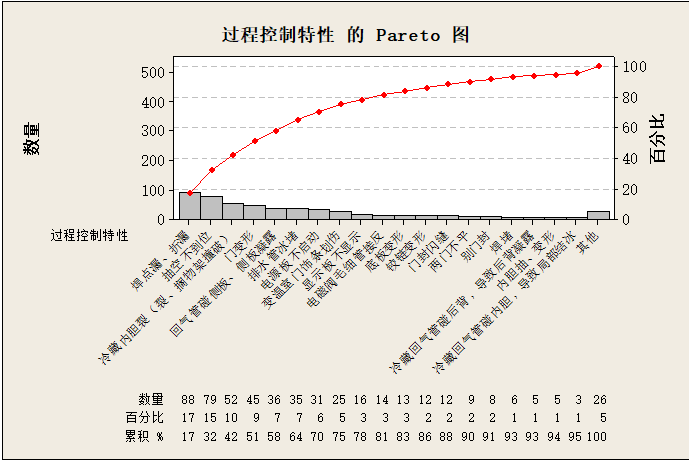
不良与特性匹配(部分)
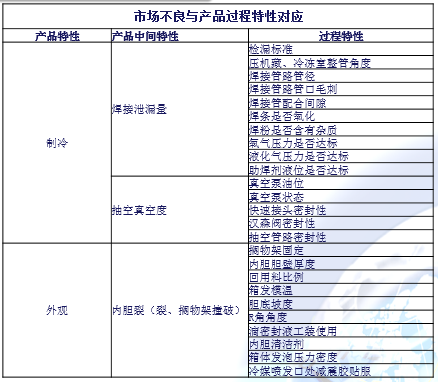
关键特性选定(部分)
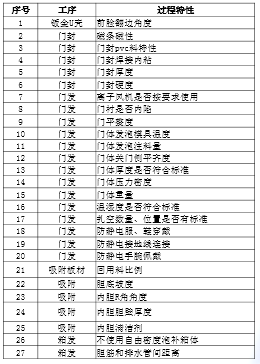
建立关键特性的SPC控制方法(部分)
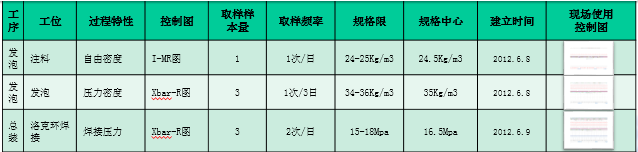
STEP3-检查(Check):
此阶段主要是对实施阶段建立的SPC控制方法的现场使用情况进行核实,主要核实的内容有:现场的实际使用情况,及在使用过程中需要改善的问题点。
过程效果巡查(部分)

现场问题点改善(部分)

STEP4-(Action):
此阶段分为3个步骤展开:产品特性的过程能力分析->过程能力改善->SPC反馈机制建立。
在实施阶段建立了的SPC控制图进行控制确保过程的输入受控后,接下来需考虑的问题是:现场管控后的输入特性能力怎么样呢?因为受控的过程并不代表是有能力的过程,所以此阶段的重点工作就是对受控的过程进行过程能力的分析,并对过程能力不符合要求的输入特性进行改善以确保其到达要求;最后的工作就是对整个SPC的控制建立反馈机制,以确保其长期有限的运行。
过程能力分析及改善
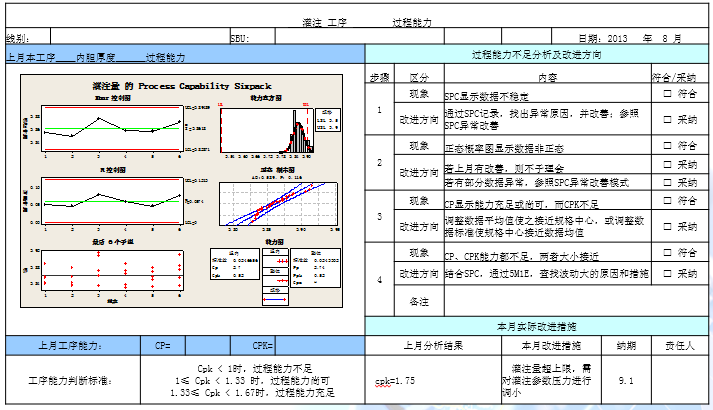
建立SPC长期管制机制
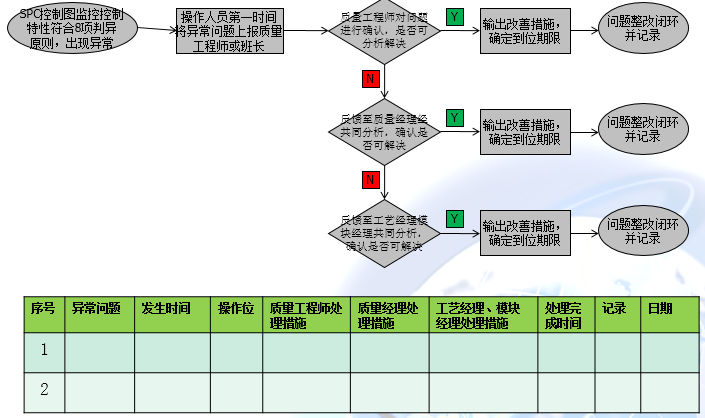
通过近5个月的时间,冠卓咨询为H企业建立了一套完善的SPC控制体系,那么这么一套完整的体系为该企业带来了哪些方面的好处了,通过以下两个关键指标3个月数据的追踪,av十大软件明显感受其带来的变化:
1.过程能力的提升

2.市场三月不良率的降低
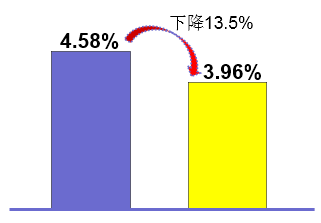
本文为冠卓咨询原创文字作品,任何人或组织不得对本文进行篡改,转载或以盈利为目的行为,一经发现,将负法律责任。