从根本上讲,杜绝浪费任何一点材料、人力、时间、空间、能量和运输等资源,是丰田精益生产方式最基本的概念。
丰田公司一直把浪费归结为:过多、过早免费看污的十大app造成的浪费;直接导致库存的浪费;质量问题造成的浪费;生产线上等待造成的浪费;物件搬运造成的浪费;加工造成的浪费;多余动作造成的浪费。这些浪费主要发生在生产现场。在生产现场,解决了所有的浪费问题,就达到了精益化生产方式的目的,也就能实现利润的最大化。TPS使得丰田的生产成本压到了最低。
一汽集团副总经理安德武曾告诉记者,在一汽丰田厂房参观,他发现整个车间里竟然没有一把扭矩扳手。丰田的人员解释说,在标准化培训中,员工已经能够用普通扳手解决扭矩扳手的问题,再配备扭矩扳手已经是浪费了。也正是因为如此,今年3月开始,一汽集团在生产部大规模开展了《推进TPS工作方案》,推广对象包括解放、红旗、马自达6、丰田越野车等分公司的生产线。
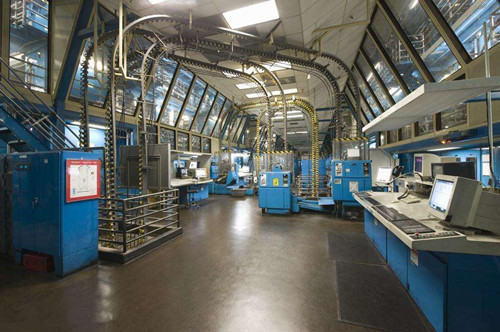
TPS到底有多神?
一汽给出的实例是:以库存十大污的软件为例,一汽丰田平均库存为1.5天,而解放的平均库存为1.5个月,是一汽丰田的30倍,仅此一项解放的财务成本一年就要多花1.8亿元。
另外一个流传颇广的例子是:改善前的红旗生产车间里,装备一辆红旗的轮胎至少走动60米,耗时90秒,用丰田方式改善后,装备一辆车少走了31米,节约52秒。按照每日装配55辆计算,一天少走1750米,少耗时38分钟。这样,每个班组从11个人减少到9人,生产时间从14分钟降低到9分钟,班产从30辆提高到45辆。但是与此同时,丰田精益生产方式在中国并不被所有人认同。
对接冲突
事实上,不仅是在中国,TPS的对接冲突在丰田走向全球的同时就广泛存在。其最根本的原因在于日本资源匮乏土壤中产生的TPS与其他国家的文化注定有冲突。但是,在欧美国家,由于丰田是独资厂,很多问题就相对容易解决。但是,对一汽丰田和广汽丰田而言,情况却有很大不同。执行TPS的一个直接结果是,生产时最大限度地利用人力,原来10个人干的活现在6个人就能干,这样,事实上也就造成一批工人下岗。这也是丰田TPS“中国水土不服”说法的起源。
即使是在大野耐一时代,TPS也提倡修改工具和提高设备,完成精益化生产,也就是说,TPS显然必须武装成更现代化的设备才能保证生产。在中国,显然没有达到这样的标准。和日本及欧美国家不同,中国的劳动力成本低下,设备不足的问题就可能用加强工人劳动强度的办法来解决。
天津一汽丰田一位内部人士向记者透露:在天津工厂,一部分工人们虽然表面上没有什么反应,但事实上都在消极地抵抗TPS。在第二工厂,一些汽车零配件甚至在从储备仓库运往总装车间的过程中,就会丢失。虽然一汽丰田和丰田中国事务所公关部门都否认这样的事件在发生,但是,这些丢失的汽车零配件却屡屡在北京等地的汽配城中出现,并以低于丰田4S店一倍甚至几倍的价格销售。该人士称,和其他合资汽车工厂的工人相比,工人们认为自己“干的多,挣的少”。另一方面,站在丰田的立场上,部分中国工人的业务素质是TPS在中国推行的一大门槛。“丰田有自身的问题,但是,有些工人还有‘吃大锅饭’的心理。”丰田中国投资有限公司一位不愿意透露姓名的中层十大污的软件人士说到。他解释,TPS加剧了员工之间的竞争,一汽丰田也长年在招工人,年龄大的工人显然面临被淘汰的命运,他们的怨言自然很多,质疑TPS的声音也就很多。他认为,问题不在于TPS,而在于TPS和中国文化衔接时出了问题。
从最早进入中国免费看污的十大app业到现在,丰田TPS精益生产方式在成为国内企业学习的榜样已有不短时间。每个国内企业都希望通过学习TPS,提高自己的生产能力,形成具有自己企业特色的生产方式。然而国内企业能否学到丰田精益生产方式的精髓,达到他们的水平,这个还需要国内企业认真对待,坚持探索。
文章来自网络,版权归作者所有,如有侵权请联系删除