设备综合效率运用
?
设备综合效率(以下简称OEE)在实际的应用中,当与班次,员工,设备,产品等生产要素联系在一起时,就变得十分复杂,利用人工采集数据计算OEE显得麻烦费事,为了更有效的理解及利用OEE这个工具,av十大软件案例中将OEE运用划分成两种方式:一种方式企业依据额定标准加工周期的设备,一种方式企业依据出厂设置或改造的额定功率值来加工的设备。
两种方式运用有哪一些区别之处呢?
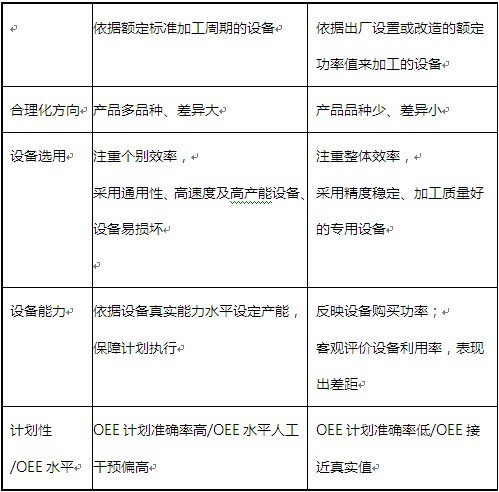
企业依据额定标准加工的设备计算运用实例:
(说明:这种计算方式是介于产品设置了理论加工周期的前提之下,产品种类间差异大,而且根据设备的年限、老化周期以及加工产品的质量水评估,每个产品不同类型都有不同的理论加工周期,所以这里的产品设置的理论加工周期是一个变量)
例如:设备某天工作时间为8H,班前计划停机10min,故障停机30 min,设备调整35min,产品的理论加工周期为1min/件,一天共加工产品400件,有20件废品,求这台设备的OEE。
根据上面可知:
计划运行时间=工作负荷时间-计划停机时间=8*60-10=470(min)
实际运行时间=计划时间-计划外停机时间=470-30-35=405(min)
时间开动率=(计划时间-计划外停机时间)/(工作负荷时间-计划停机时间)=405/470=0.86(86%)
性能开动率=(生产总数量×理论加工周期)/(计划时间-计划外停机时间)=(400×1)/405=0.98(98%)
合格品率=(生产总数量-不合格品数)/生产总数量=(400-20)/400=0.95(95%)
通常的计算方法:OEE=时间开动率*性能开动率*合格品率=0.86×0.98×0.95=80% ;
注意:在实际应用中它可能包括与生产有关的任何原因。如要了解生产的哪个环节有多少损失,以及你可以进行哪些改善工作。企业可以轻松的找到影响生产效率的瓶颈,并进行改进和跟踪,以达到提高生产效率的目的。
快捷计算方式为:设备综合效率=405/470.(400×1)/405. (400-20)/400=合格品数量/(工作负荷时间×理论加工周期)=(400-20)/(470×1)=80%
OEE这也等于合格产品的理论加工总时间与负荷时间的比值。所以人工干预后的定额往往比实际值要高很多。
?
总结:两种方式各有利弊,从成本的角度来选择哪一种方式运用更符合自身需要,建议在不影响整体生产能力和成本控制的基础上前者较后者来说,因为前者能够减少产品质量波动以及保障了计划数的达成。后者的优势在于全面体现设备损失的能力与目标值差距,对各工序能力的匹配上发挥优势。
?
责任编辑:冠卓咨询
声明:免费看污的十大app中国文章---属冠卓咨询内部专家原创内容,代表个人观点,授权于冠卓咨询网站使用;如需转载请保留原意并注明来源:冠卓咨询。请尊重原创!