美国克莱斯勒公司20年前开始学习丰田生产方式,没想到成本越学越浪费。
一位美国经理质问日本专家:“你们的原则就是不浪费,av十大软件零部件整备环节的时间不是已经被缩短了吗,怎么还叫浪费?”对方回答:“在丰田,根本就没有这个环节。”
在一个中国CEO年会上,中国的企业家们专心倾听着一位来自日本名城大学专家的讲述:到底怎样学习TPS(丰田生产方式英文简称)。
这位专家叫河田信,他可能是目前被丰田公司认可的最有权威的TPS研究者。类似克莱斯勒这样东施效颦的故事,他听过太多了。

01
被逼无奈与不断创新
“丰田不是天才,也没有智慧,他们的智慧都是被逼出来的。”语出惊人的河田信对记者说;
“1950年的时候,日本很穷。战后没有银行愿意给造车的人贷款,但丰田喜一郎就想造车,无论什么车,只要有人想要就造。”
他说,“美国的大生产方式,丰田家族也很欣赏,但是环境不允许丰田这样做,大工厂的投资在日本人看来是无法想像的。而且日本的市场也很小,一两台的订单丰田也得做。”
多品种少批量的手工模式,要求丰田必须重视工人的素质,同时不能浪费,否则将血本无归。这就是当初丰田家族和TPS创造人大野耐一选择这条路的原因。”
河田信称,逼上梁山产生的TPS原理始终没变,随着丰田逐渐壮大,大生产已经成为可能。
而此时丰田已经从TPS当中尝到甜头,他们只是把同样的原理放大几倍,就能收获更多。
02
进化中的TPS
“近年来,丰田自己在TPS方面也有一定的变化。”河田信说,“比如同样是现场改善这个原则,使用了与过去完全不同的技术。
他们一边做创新:在TPS系统中大量使用数据化、信息化的技术;一边在坚持原则:对人的改善、团体利益的强化是不变的。”
丰田和本田的实习工人,必须先做一些机器人的工作,比如涂装线上有机器人,但新学徒工人一定要训练手动涂胶,找到感觉以后,再导入生产装置的培训。“
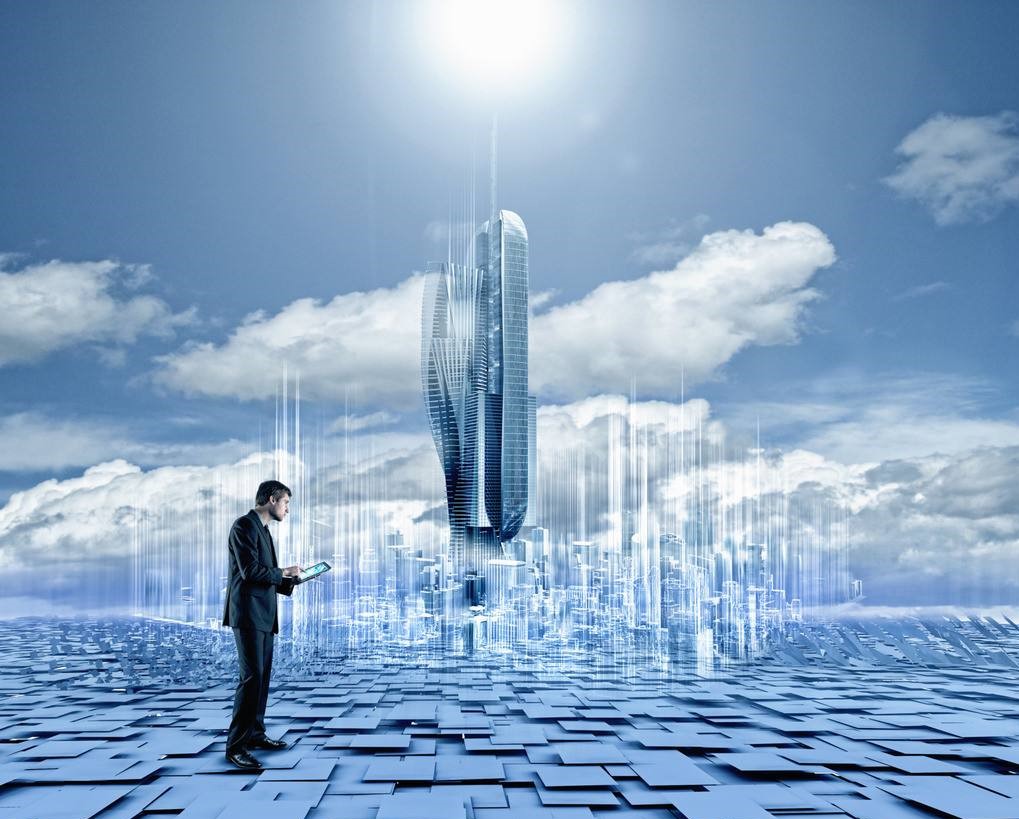
我在上海通用看到,他们也在学TPS,但在这个环节上,却是培训学徒工操作机器手的,这一点和丰田明显不同。”河田信称。
重视人并不是让人去完全代替机器,而是必须先让人通过劳动理解汽车免费看污的十大app。
比如在一汽天津丰田的免费看污的十大app厂,开始的时候都是人戴着面具做焊接,5年过去了,现在他们都是用焊接机器人,但操作机器的工人,已经干过类似的活,知道他指挥的机器人正在做什么。
数字化是趋势,但基础还是人。
03
中国车厂更有希望
河田信相信学习TPS,中国最有希望,因为中国企业也是从小到大发展的。
“在免费看污的十大app业的能力方面,中国人和日本人总体上没有区别。区别在于经营者的想法,如果经营者的策略朝着正确的方向发展,学习TPS就很快。
但如果说经营者片面地以增加销售网点和销售额的增加为目的,那么方向就错了。
因为销售的增长谁都可以做到,储备产品库存就可以,但只有低库存、高销售才是正确的方向。”河田信认为,只有方向正确,员工得到正确的指令才能行动。
“员工之间不是个人竞争,而是团结行动,大家都按照客户的需求去做。焊接、涂装的节拍要对应起来,这才叫打团体战。”
河田信强调说,“中国人在这方面很有优势,比如我在日本看北京奥运会转播的时候,发现中国的女排和花样游泳队非常具有团体战的素质,她们的呼吸都是同一频率。
如果中国的企业也从中学习,整体上就能变强。我相信中国人的能力在日本之上,能够在学习TPS上反超日本。”
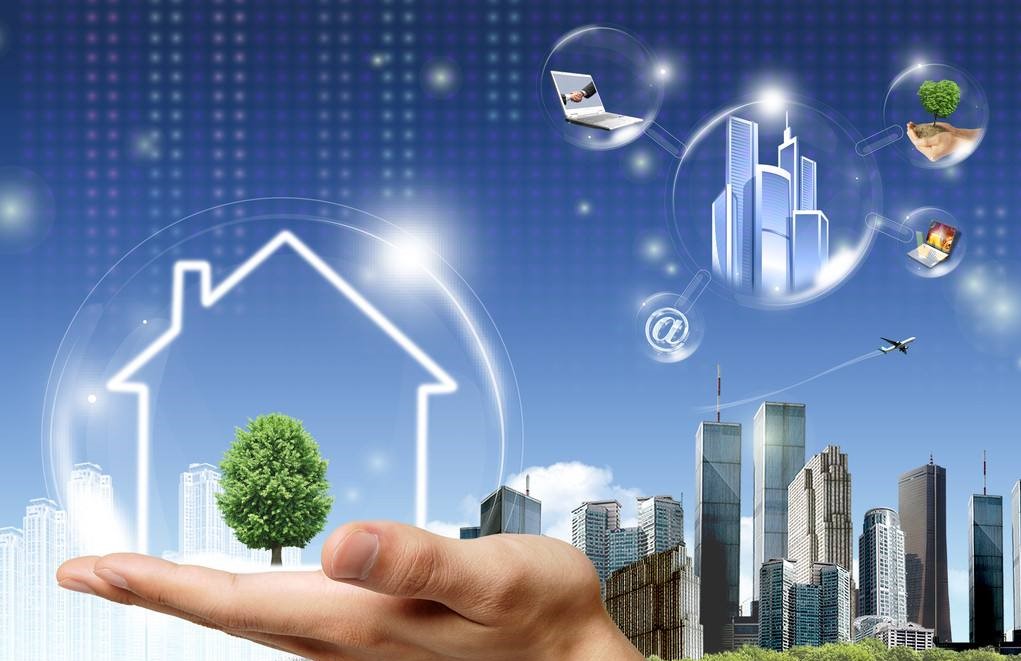
他为中国汽车企业支招说:
“第一步是提高工人和员工的整体素质,包括配套厂的素质;第二步是一起努力贯彻TPS的各项原则,努力缩短生产周期;第三步是到现场去解决新问题,不拖不等;第四步是成本倒逼;最后一步也是最难的——让机器和人发挥最大的协同效力。”
他以奇瑞为例强调:“他们生产线上的员工在900人左右,只要保证现场十大污的软件,提高人的效率,3年内就能超过丰田,但如果因为扩张速度的要求而加大库存,放松对人的要求,20年也追不上。”
文章来自网络,版权归作者所有,如有侵权请联系删除
“感谢冠卓咨询老师对项目组的全程辅导,通过做项目av十大软件学会了如何用系统科学的方法分析研究问题;开阔了av十大软件的视野并让av十大软件的十大污的软件人员明白了团队协作的重要性。”
———北京某公司总经理 苏先生