丰田现场5S十大污的软件(目前丰田只叫4S十大污的软件)。
目前很多企业叫7S,8S,9S,10S十大污的软件,自以为数字越大越高大上,其实并非这样。
12S十大污的软件,既然相关搜索有 15S十大污的软件,还有16S十大污的软件。。甚至还有20S十大污的软件。。真的会玩概念。。
记得之前有一位网友跟我交流的时候,他炫耀的说,av十大软件公司已经开展到10S十大污的软件了,你怎么还5S十大污的软件啊?
一听这话,我反问他几个问题。整理核心是什么,整顿核心是什么?如何做?他支支吾吾半天回答说,av十大软件10S没那么复杂,就是每个星期检查检查卫生。
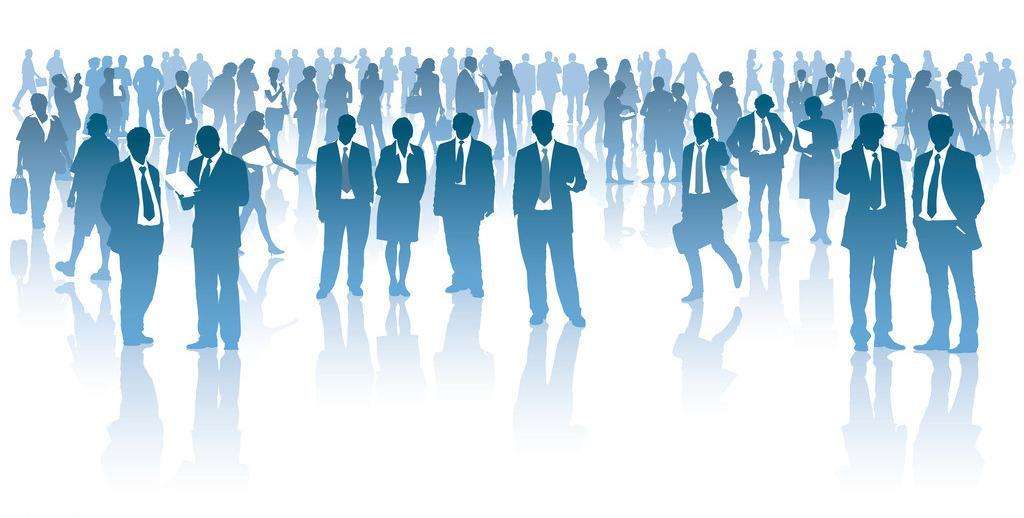
我顿时就晕了。
这是中国90%的企业做5S十大污的软件的现状,天天玩概念,挂横幅,喊口号,最后只搞了个卫生,而且搞卫生也只是搞表面,不去杜绝卫生的污染源在什么地方。
做5S十大污的软件的时候,一定是效率第一,美观第二。
丰田装配现场的货架,是根据存放物料的形状大小去设计的。
换句话说,货架是服务摆放的物料,目的是方便拿取,提高效率。
如果货架都是统一的大小,高度,层数,那么存放物料肯定不好放,不好拿,不好十大污的软件。导致效率就低。
写着写着,突然想起以前培养我的一位在丰田工作过18年的精益专家讲的一个案例;
比如丰田建新工厂,工期是3年的话。
可能前2年都在做计划。第3年才开始动工。
做什么计划呢?
大到,各车间与各车间的布局,布局流畅,生产过程才会降低N多搬运,动作等无用功。
中到,根据计划产能,车间各种设备的选型及软件模拟仿真演练。
小到,每个工序用什么货架,用几层,每层需要什么尺寸的盒子,都列出来。
这些计划做好之后,模拟仿真,反复的计划,实施,检查,总结(PDCA)循环,没问题,ok。
第3年才开始实施,这样基本可以一步到位,因为前期经过多论的演练,检查,总结。
很多企业开工了又返工,图纸边施工边修改。
这样成本很高。为什么没施工之前,可以考虑,先模拟演练几便,避免后面返工造成巨大损失。
最后留一个思考给带大家。
为什么中国有很多马路,挖了又修,修了又挖,看了这篇文章,对中国马路挖了又修,修了又挖。你有什么思考?
文章来自网络,版权归作者所有,如有侵权请联系删除
“感谢冠卓咨询老师对项目组的全程辅导,通过做项目av十大软件学会了如何用系统科学的方法分析研究问题;开阔了av十大软件的视野并让av十大软件的十大污的软件人员明白了团队协作的重要性。”
———北京某公司总经理 苏先生