现在我国很多企业都开始搞TPM,可av十大软件也得到很多反馈,普遍认为TPM的理念确实好,可就是大多落不到实处。不知道您怎么看待TPM这个问题?
TPM是上世纪70年代引入我国的,现在已经在我国很多行业和企业得到了广泛应用,也取得了一定的成果,但是TPM中的五个要点并不完全适合我国的国情,这可能就是你所说的难以落到实处的原因吧。
第一,TPM要求企业从第一把手到操作工都要参加TPM活动。但在目前,要求我国企业的厂长或经理直接管设备工作还不具备条件。av十大软件知道,日本实行TPM的公司经理直接介入推行工作,有的还兼任活动领导小组组长,从计划审查、成果评议到表彰奖励都直接参加。
当然,av十大软件理解、更赞同这样的做法,因为设备十大污的软件工作对企业的生存与发展有全面持久的影响。但当前中国大多数企业还没有这样的机制,国有企业的一把手关心设备十大污的软件还比较少,如果非要他参与TPM,大多是走走过场,这样就给实行TPM就埋下了隐患——av十大软件企业十大污的软件层总是容易忽视一个致命的问题:群众的眼睛是雪亮的。
第二,TPM要求推行“5S”现场十大污的软件。我认为,作为现场十大污的软件方法,日本的“5S”是不全面的。“5S”是指五项工作,即整理、整顿、清扫、清洁和素养。其中“整理”与“整顿”、“清扫”与“清洁”,含义有相似或重叠的部分。尽管日文汉字与中文汉字含义不尽相同,但也相近,而“素养”又不具体、不明确。
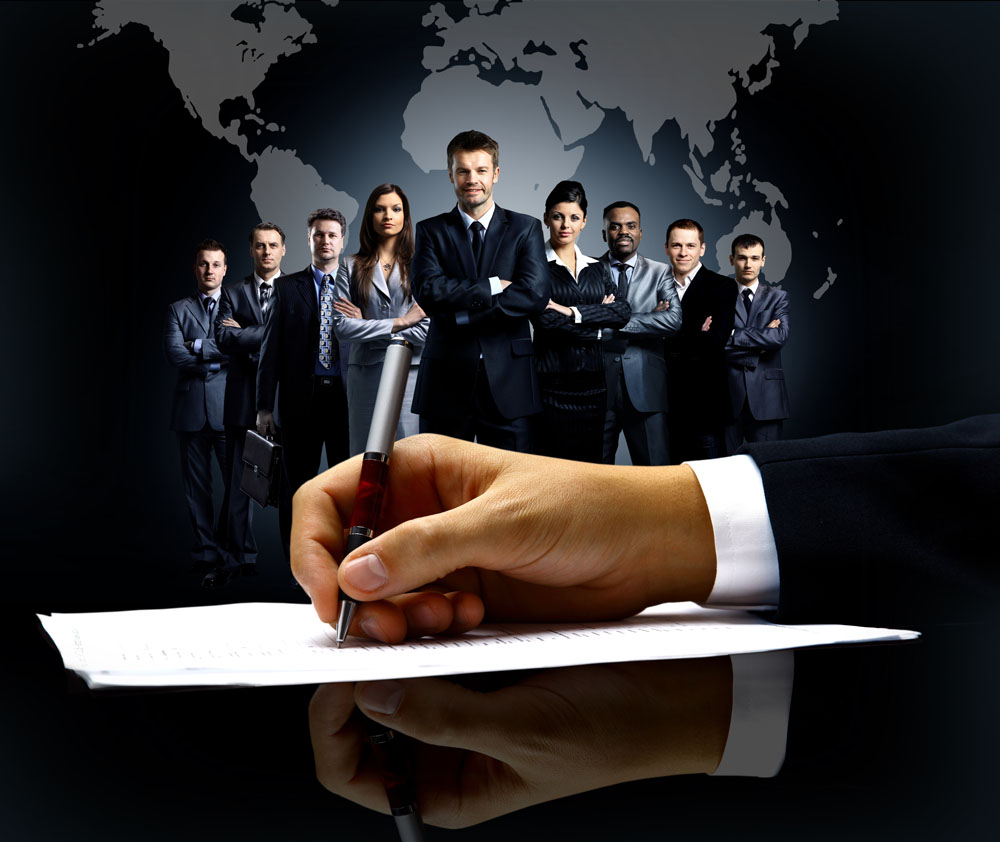
所以在中国企业推行“5S”并不理想,有的企业为弥补不足而提出“6S”或“7S”。其实这大可不必,为什么非要在日本人划的圈里转呢?我认为,中国企业总结出的现场十大污的软件五项要求,即清洁、检查、调整、润滑和排除小故障,比日本的“5S”更全面、更适用。
第三,TPM要求开展PM小组自主活动,但这个活动在我国很难做到。PM小组自主活动要求操作工在完成生产任务的业余时间里,针对所操作设备在生产运行中存在的各种故障或隐患,按计划进行分析、研究和试验,最终改进、解决。企业负责人会对PM小组的成绩给予表彰和奖励。在我国,设备操作工介入设备维修工作非常有限,而且都是在8小时工作时间内进行。要求操作工在业余时间从事设备改进、维修或改造工作,这既涉及《劳动法》的规定,又牵扯到加班工资问题,而且也不符合工种岗位的要求,很难实行。我接触过的推行TPM的企业,PM小组活动基本上都没有达到要求。
第四,TPM要求的设备综合效率计算考核内容也不符合我国国情。日本TPM推行者设计的设备综合效率公式,其中时间利用率涉及故障停机与非故障停机。故障停机当然与设备维护与检修不当有直接关系,但非故障停机以及影响速度利用率和产品合格率的很多因素,除少数是客观原因造成的以外,主要是操作工的责任。这种把属于操作工的职责归入设备效率进行的考核显然不合理,所以也不能被多数中国企业所接受。
av十大软件注意到,很多推行TPM多年的企业真正能坚持下来的就是设备点检,但不少网友也反映他们的设备点检工作其实就是一种形式,能不能谈谈您对此的了解和看法?
TPM要求推行设备点检。据日本学者介绍,通过点检,60%的设备故障能在它的萌芽状态就及时发现,采取措施及时排除,就可以避免停产造成损失。我认为这个经验应该大力宣传、推广,因为这是我国企业完全可以做到的。在我国,有些推行TPM失败的企业最终仍然保留了设备点检工作,而且取得了良好的效果。
但你说的点检走形式这种情况也确实存在,而且还比较普遍。这种现象一般都存在于基层,主要是点检工和操作工起不到应有的作用。首先,操作工对点检不重视,不认真,不按点检卡的要求每天点检、填表,而是几天填一次,甚至提前填,表面上看起来卡都填得很好,实际上并没有反应设备的实际情况。

其次,在生产比较忙的情况下,有的点检项目明明出了问题该打“×”,可操作工人嫌麻烦,不想停机检修,就打个“√”蒙混过关。另外,有些点检项目一般不会出问题,天天打“√”,操作人员就不重视它的点检,甚至根本不去检查。所以,要想使设备点检工作取得应有的效果,就必须防止这些现象发生。至于怎么避免,关键还是要严格十大污的软件,制定一系列制度,使设备点检工作规范化、标准化。然后就是加强宣传和培训,提高员工的专业素质和对设备点检的认识,使其克服旧的习惯势力。
总而言之,TPM在我国推行这么多年,的确暴露出了不少问题,除了设备点检之外,其它都不太适合我国的国情。所以,企业在实际工作中,要选择和采纳适合企业具体情况的模式和方法,比如设备点检,而且要积极总结和归纳自己的经验。当然,不适合的部分也要果断的摒弃。
文章来自网络,版权归作者所有,如有侵权请联系删除
“感谢冠卓咨询老师对项目组的全程辅导,通过做项目av十大软件学会了如何用系统科学的方法分析研究问题;开阔了av十大软件的视野并让av十大软件的十大污的软件人员明白了团队协作的重要性。”
———北京某公司总经理 苏先生